THE ROTOR REVOLUTION
A NEW SPARK
Based on the experience with stump grinders and a narrow disc, Artur Willibald worked on an idea to widen the rotor for other purposes.
After the first trials and experiments in 1988 he developed the first rotor tools with carbide tips for maximum cutting performance in christmas tree plantations.
At that time, nobody even thought about using such a rotor in the ground for subsoiling or mine clearance applications.
Let’s look back …
Farming
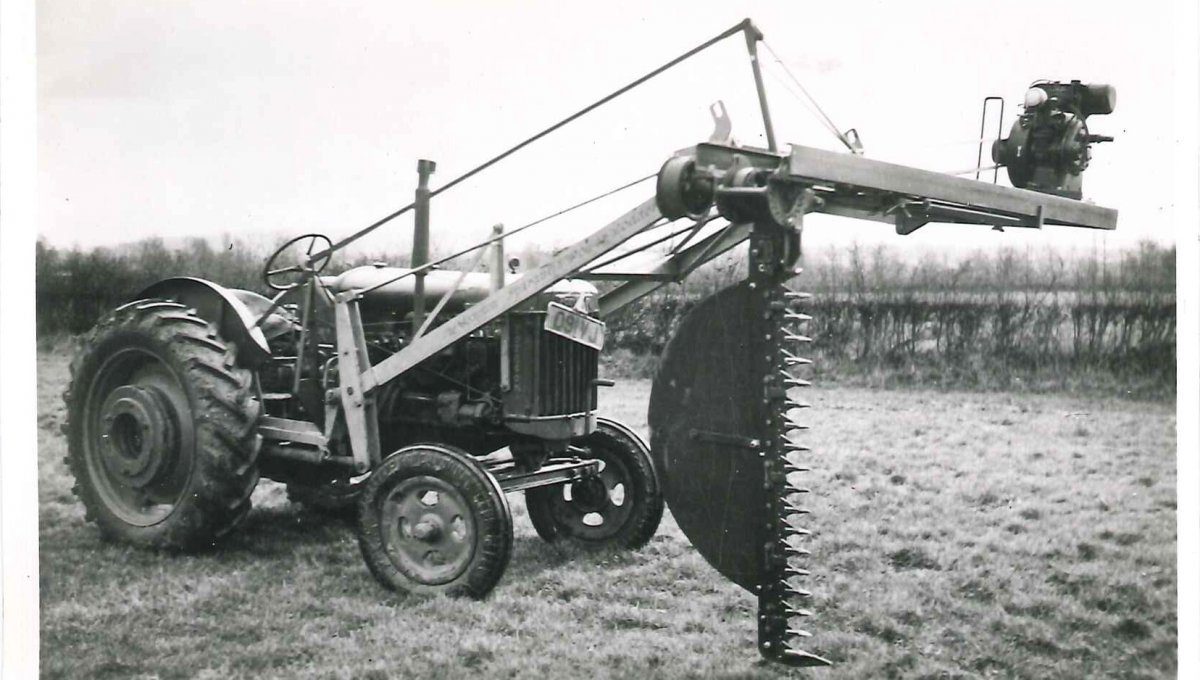
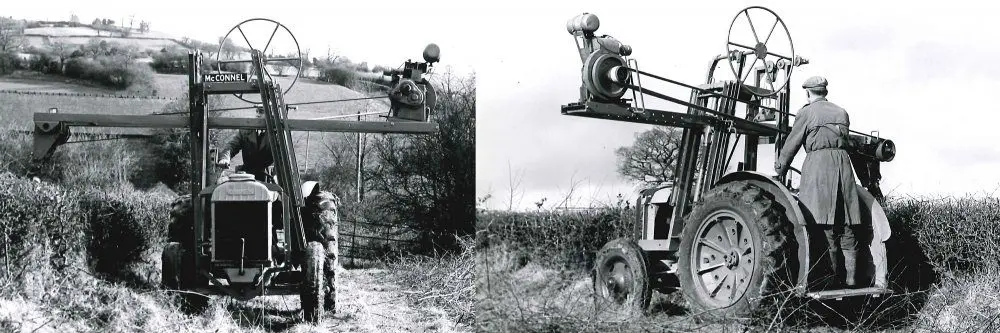
1948
Around 1945 farm tractors started to be equipped with mechanical drive auxiliary power positioned at the back. In 1948 a Scottish farmer named Gilmour invents the Mid-Mount Mark I hedgecutter and sells the rights to McConnel to build the machine. The machine revolutionises hedge-cutting offering huge improvements in speed and efficiency against manual cutting
1956
Flail brushcutters first appeared in the mid-1950s.
The first machines of this type were developed and put on the market a few months apart in France by M.Rousseau, followed shortly after by a certain Mr. Joseph Willibald, in Germany, in 1956-57.
1963
In the United States, Engler manufacturing in 1963 and Mott were combined to become Alamo, which were among the first to offer this type of device in North America.
1968
In Germany, Josef Willibald developed the first flail mower. Its improved shredding of green material now made organic viticulture, fruit growing and agriculture possible on a larger scale.
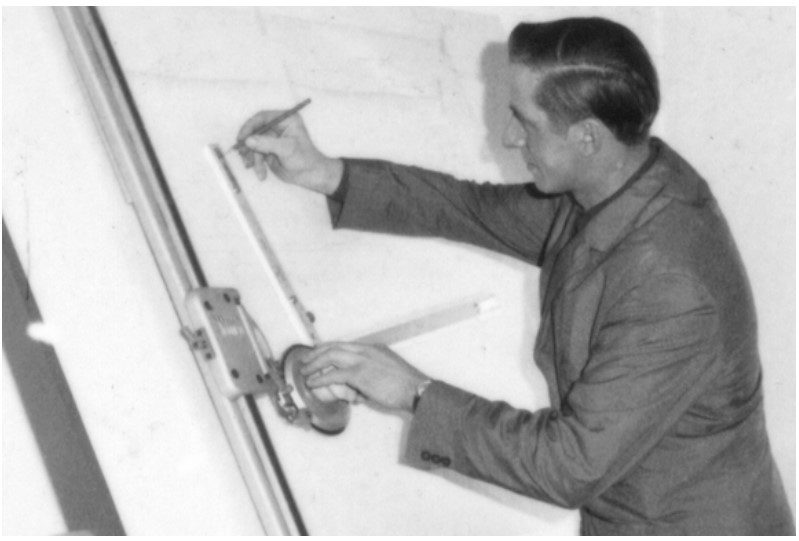
The first mulchers or known as flail mowers, launched as SM-Series in 1968, were already characterized by a robustness and solid construction that was unique up to that time and made Willibald an example of above-average quality.
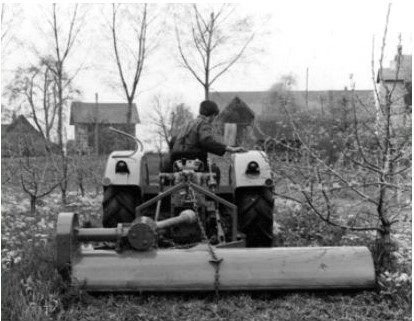
The flail mower gets its name from the use of flails attached to its rotating horizontal drumand flails are attached to it using chain links or brackets.
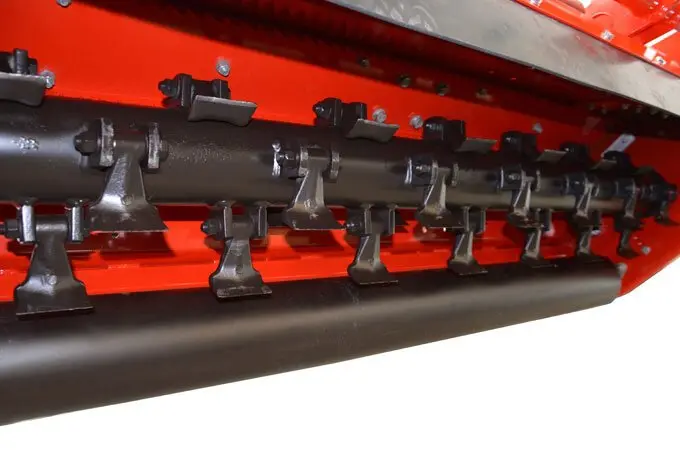
1991
Through the development of the new rotor system, grinding of stumps and roots and their mixing into the soil to fertilise it for subsequent usage became reality. With the subsoiler or rotovator, a new machine type was created to process forestry, agriculture or infrastructure areas.
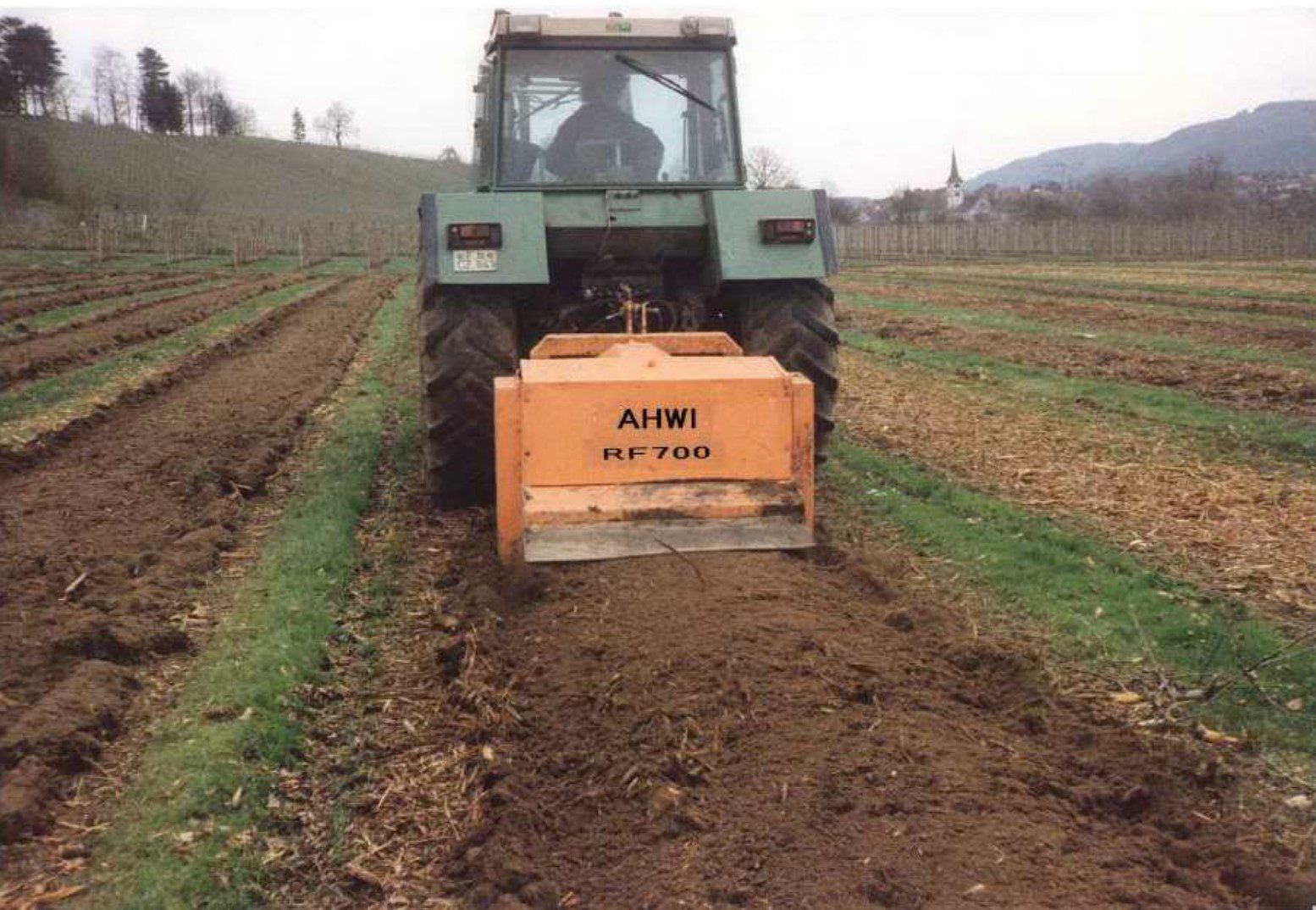
By using the new rotor style and tools with less resistance Artur Willibald could proof that this new concept would be a great success in fruit plantations. The lower rotor rpm and special chain driven drivelines could withstand the forces created if working IN the soil.
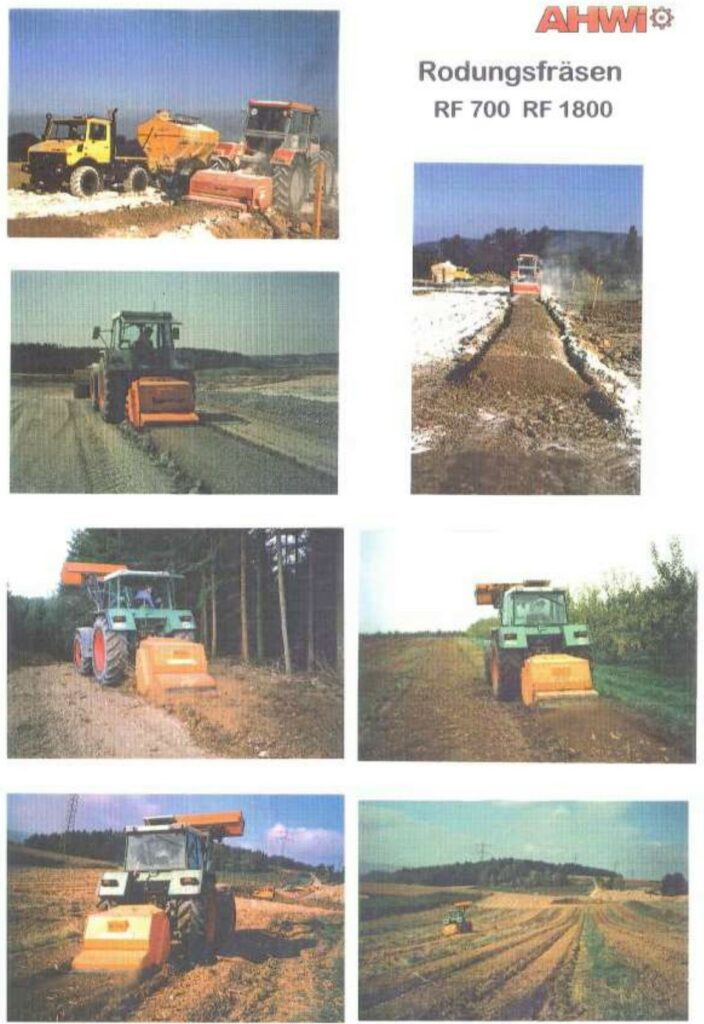
The basic rotor principle was used for many decades and rotor teeth had been updated and shaped which paved the way for agriculture in many applications until today.
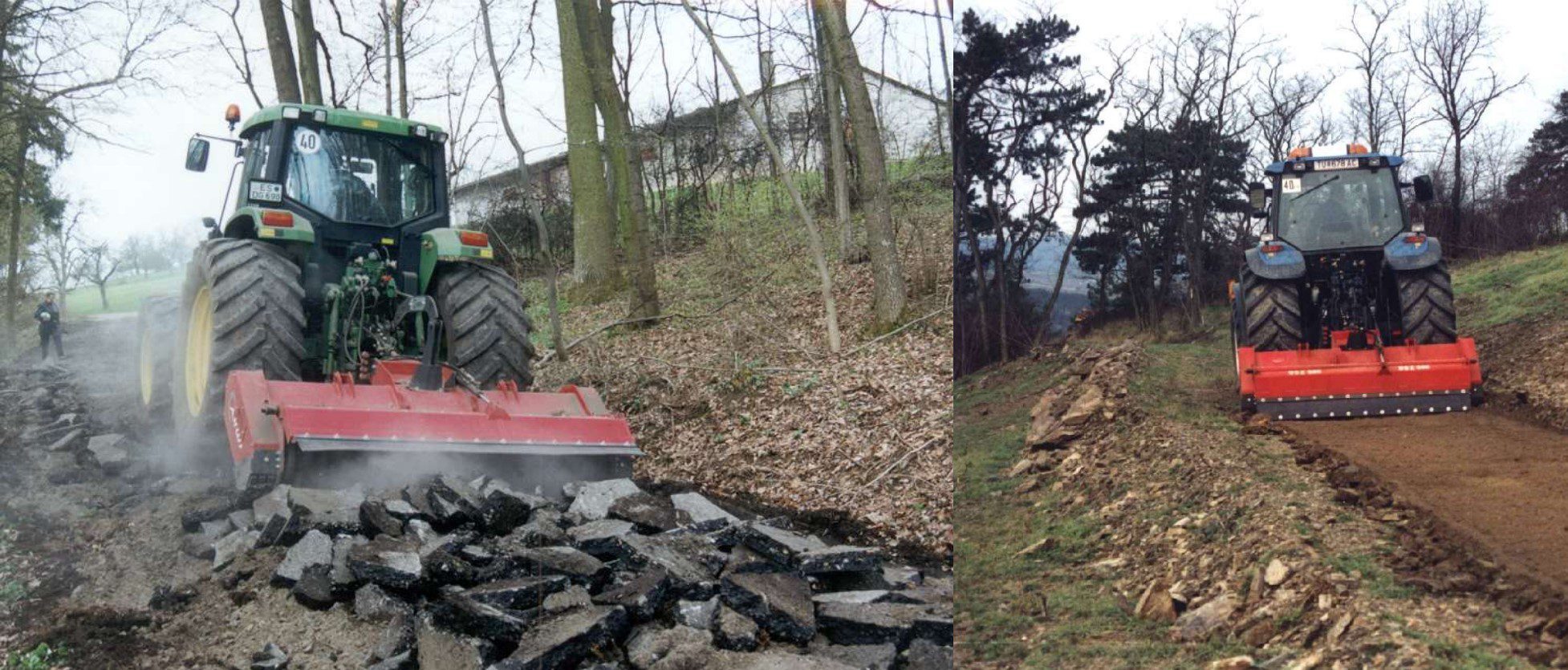

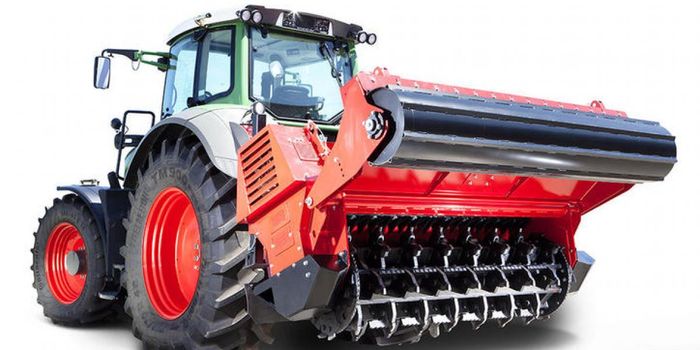
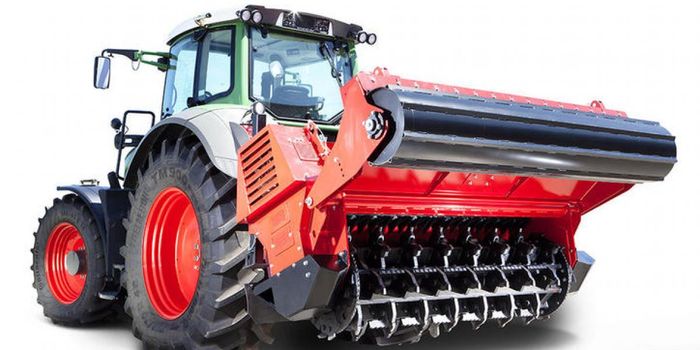
FORESTRY
The classic method of forestry mulching, was cutting, stacking and burning. Also known as the “slash & burn” method and it took another 20 years from the brushcutter until mechanization was developed enough to initiate first trials in forestry applications.
For other riskier jobs, maintenance under power lines for example, the use of chemical defoliants was common. The risks of causing forest fires and environmental issues put additional pressure to find new solutions.
All brushcutters, whatever the brand or model, had the same limitation: as their name suggests, they were originally designed to cut brush and shrubs up to 10 cm in diameter at most.
It was therefore necessary to find a way to be able to shred trees of larger diameter whose commercial value was negligible and which one had anyway to clear for the lines of transmission of electricity, corridors for the gas pipelines, or to make new roads or urban development.
1973
One of the pioneers was an entrepreneur from Owatonna, Minnesota, who developed his first units around 1965, and who, following an alliance with Pettibone, built the first dedicated hydrostatic vehicle in 1970, and which was marketed by a new company under the name of Hydro-Ax in 1973.
A forestry mulching machine, also referred to as a forestry mulcher, forest masticator, or brushcutter, uses a rotary drum equipped with steel chipper tools (“teeth”) or blades to shred vegetation.
1989
in Germany the nephew of Mr. Joseph Willibald, Mr. Artur Willibald and his brother Hubert founded the Company AHWI Maschinenbau GmbH.
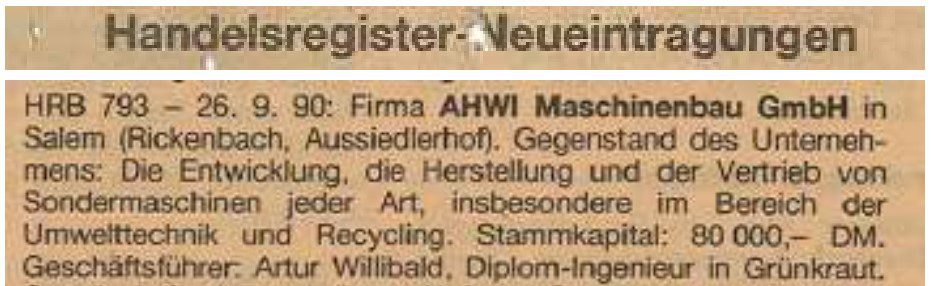
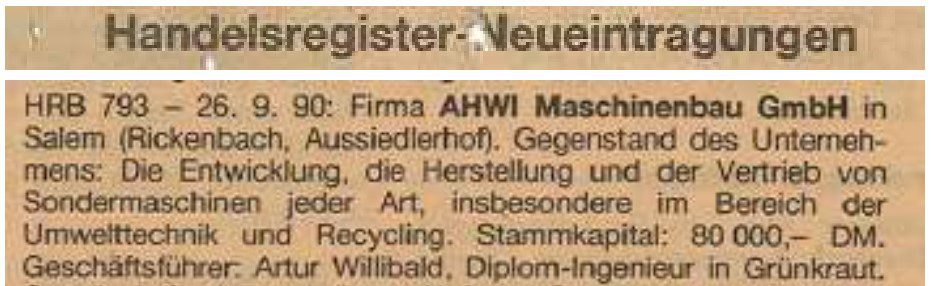
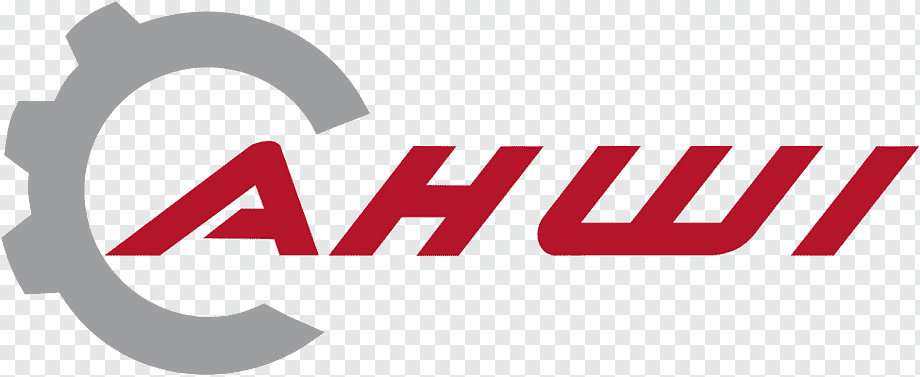
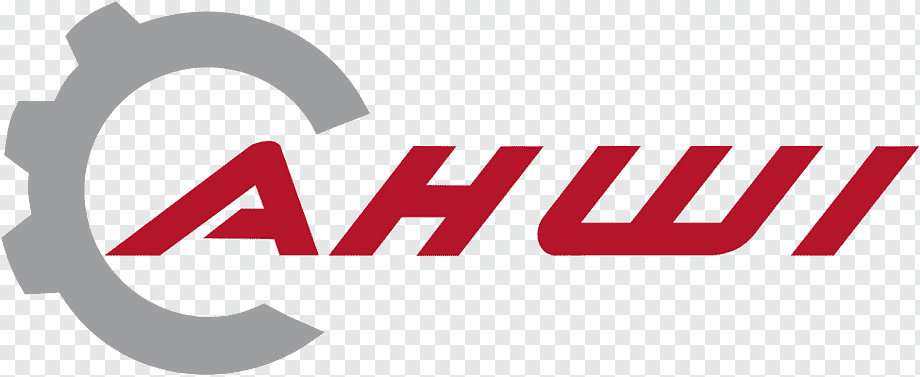
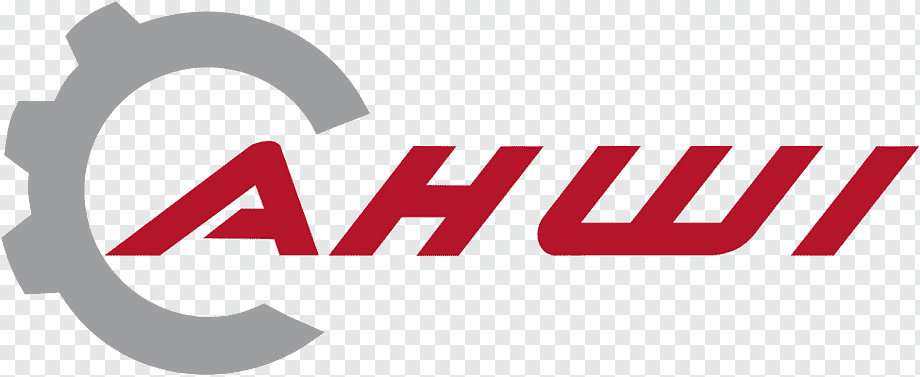
The AHWI company had roots in the agricultural world, and the vast majority of their products were first designed for mechanical power take-off (PTO) drive, like most other European companies, which made that brushcutters were first known as devices mounted on three points of agricultural tractors, with mechanical drive. The first prototype of a forestry mulcher was built in 1989 and launched for the German market in 1991 as UZM580.
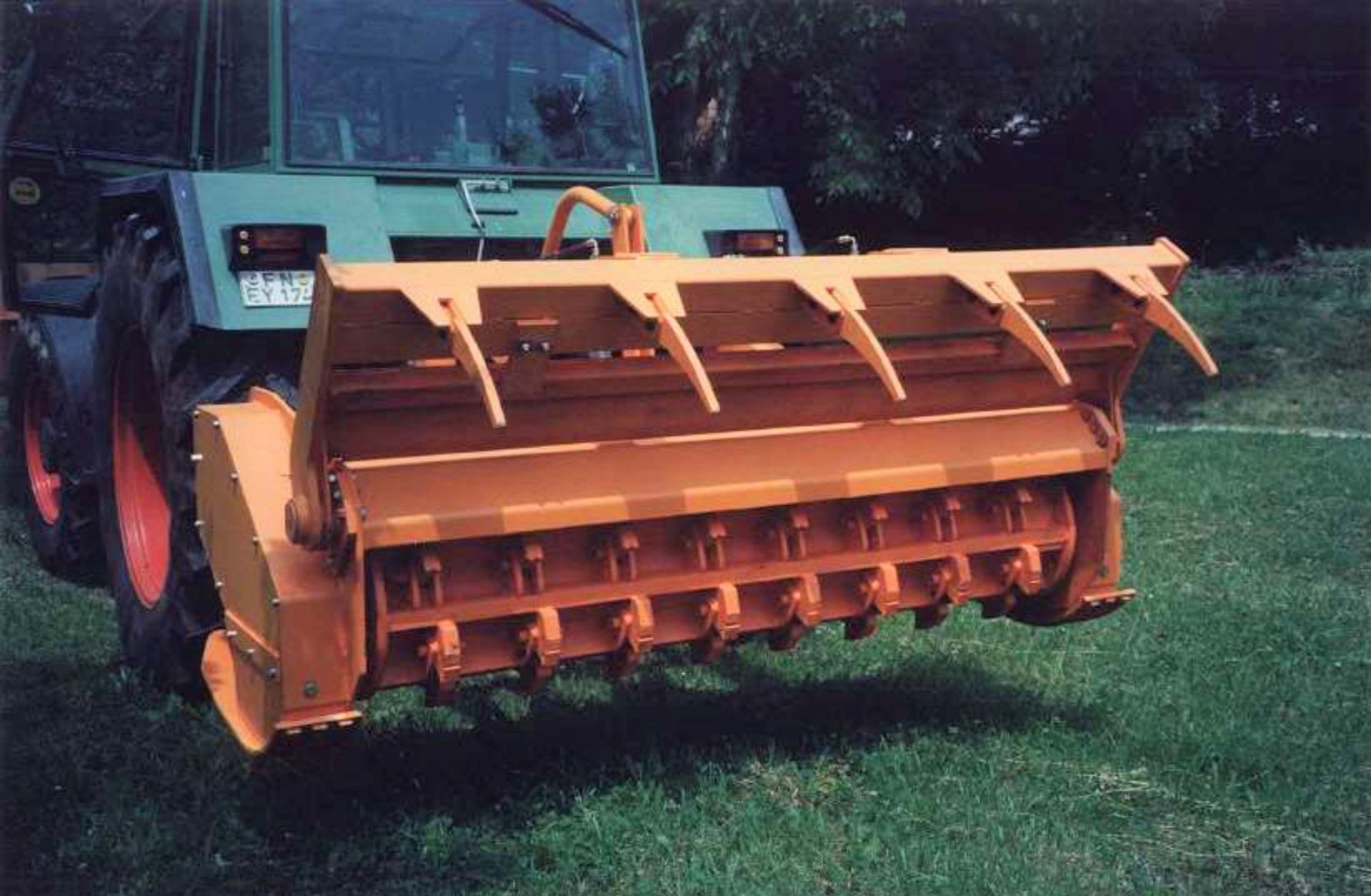
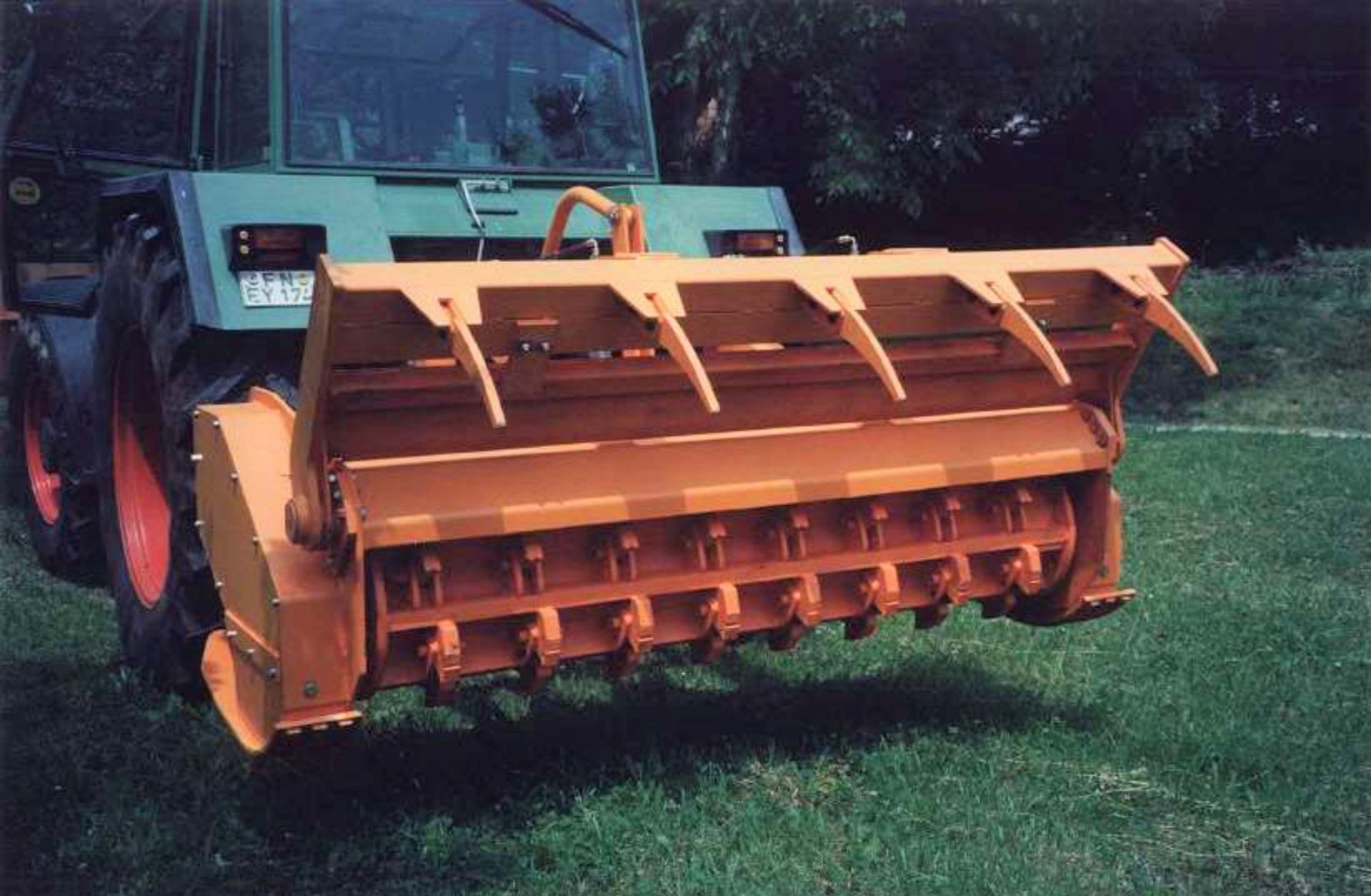
The major success of this machine was based on a flat bar rotor design with BP-2 tools and carbide tips. The double-sided drive-line and the rotor were driven by polybelts.
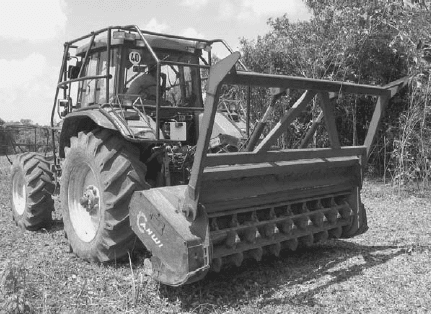
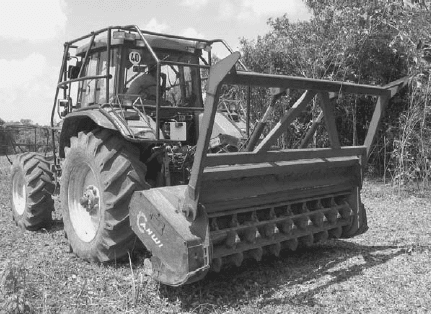
1995
Around 1994-95 the concept of mulching with fixed hammers and carbide tips was adapted by the company FAE from Italy.
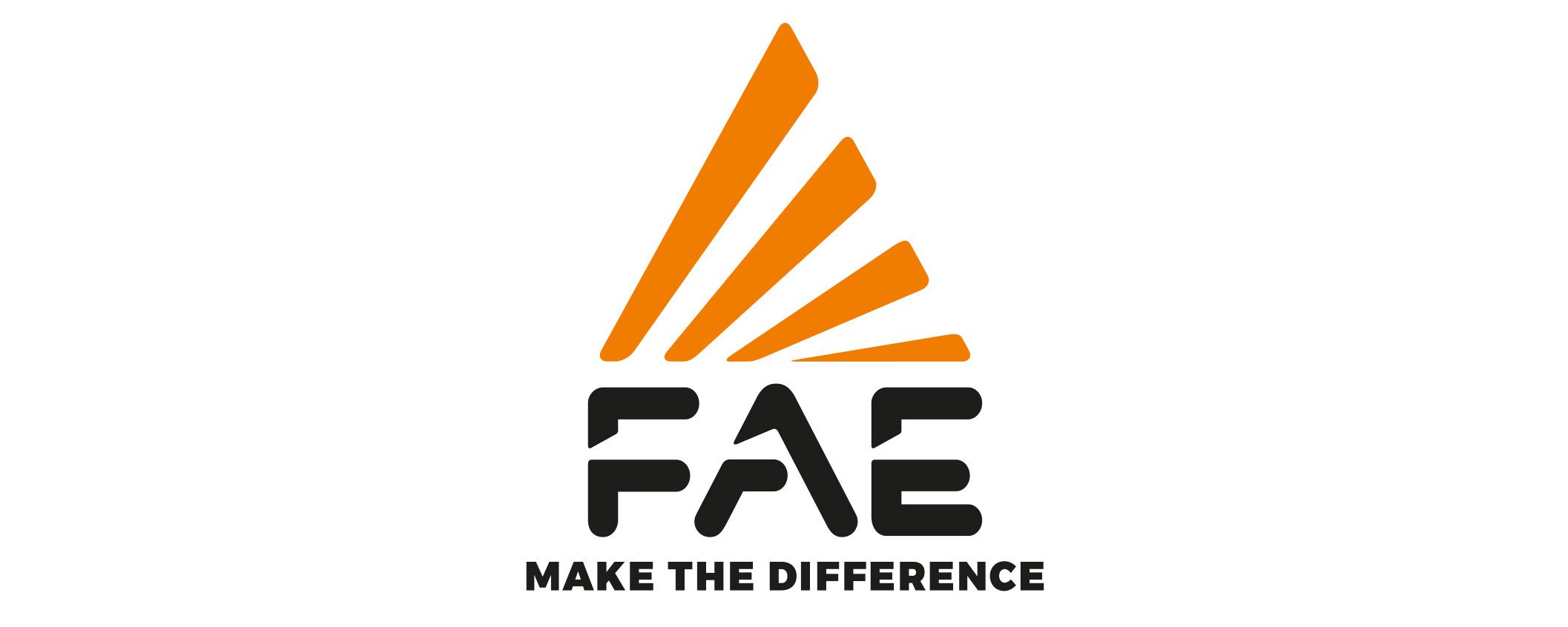
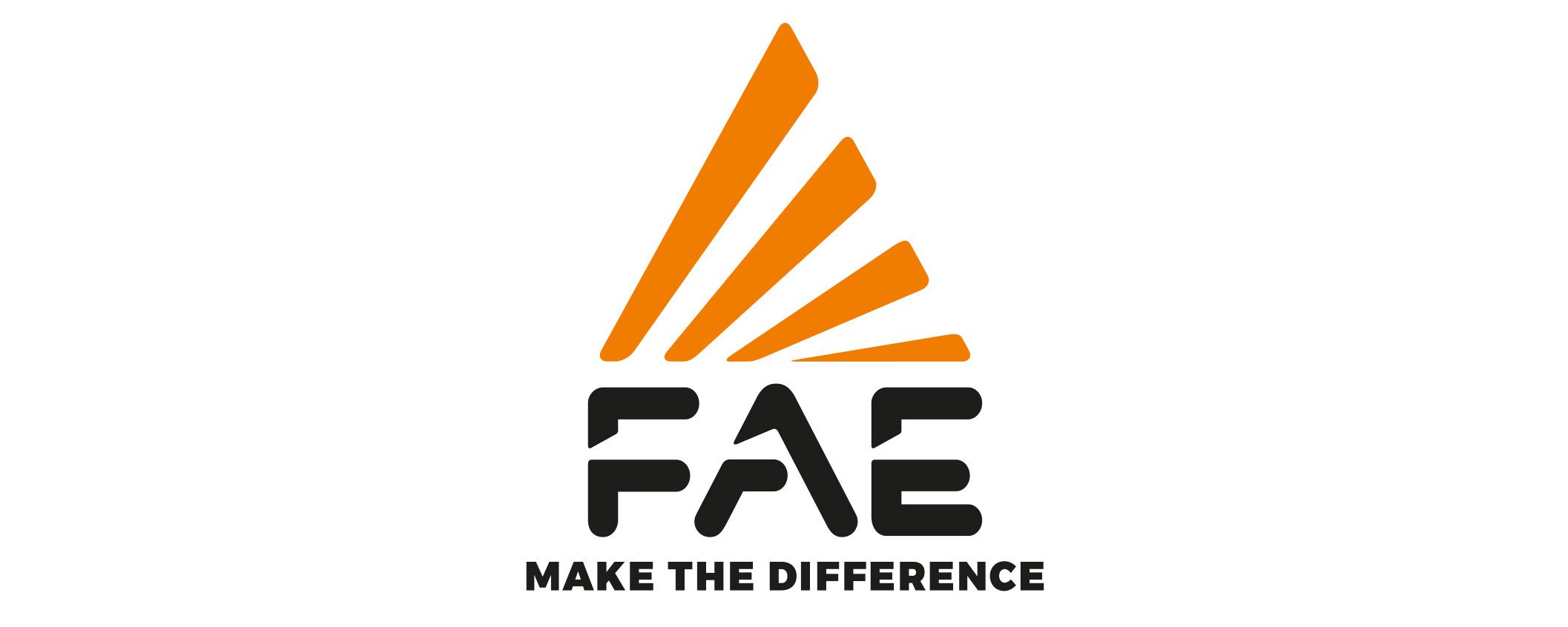
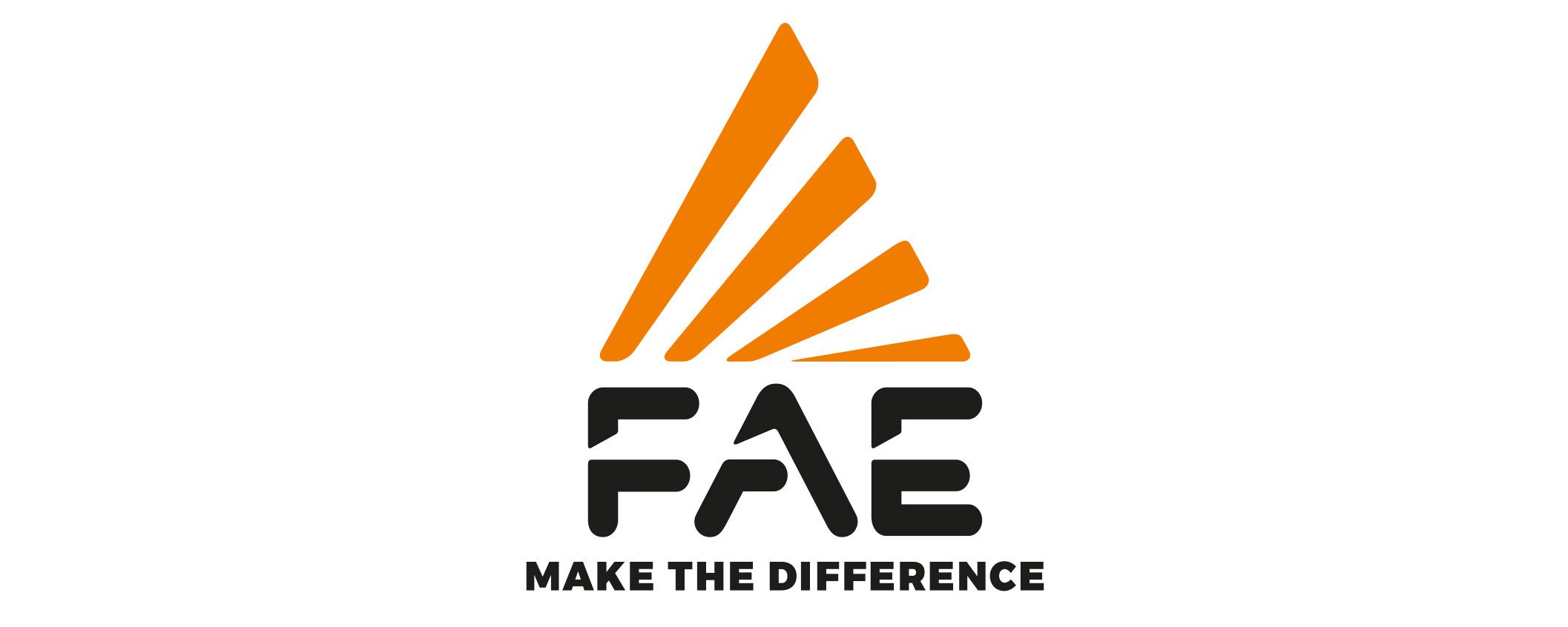
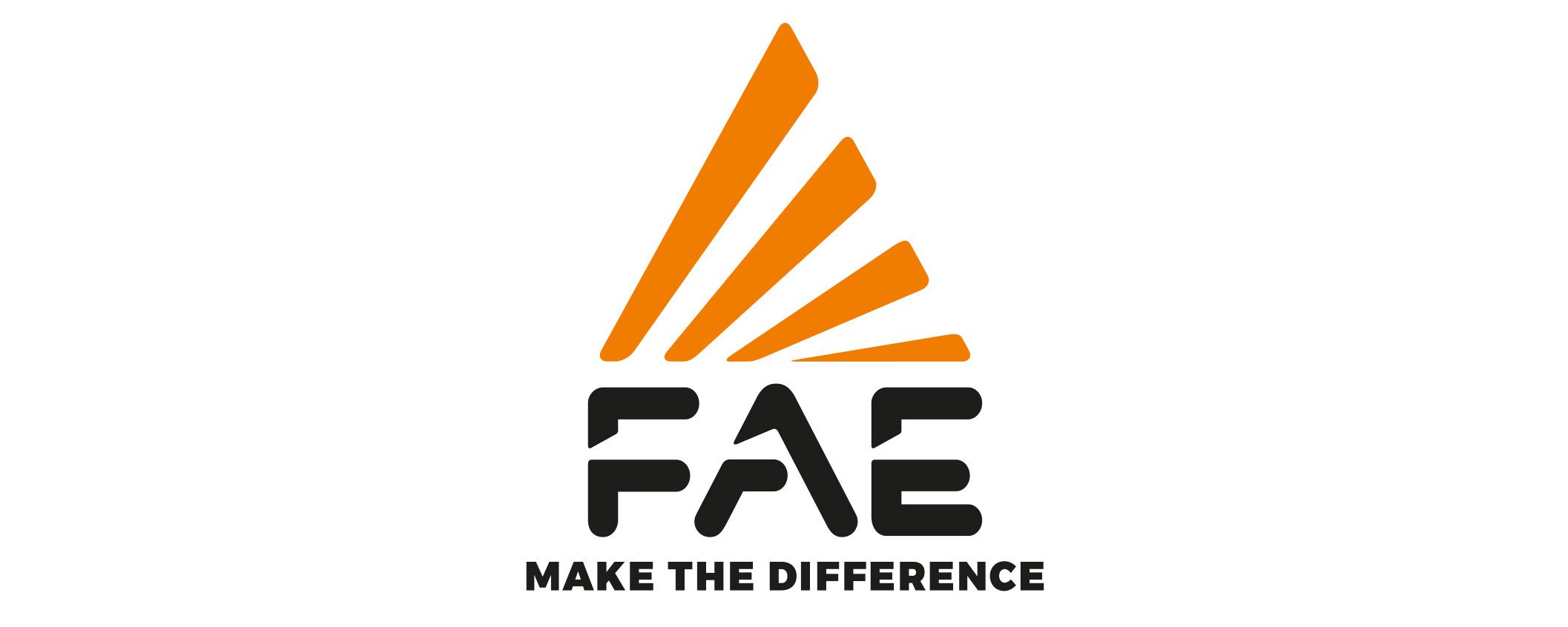
In North America, FECON subsequently obtained licensed technology from AHWI as The fixed carbide hammer crushing method made it possible to crush much larger trees.
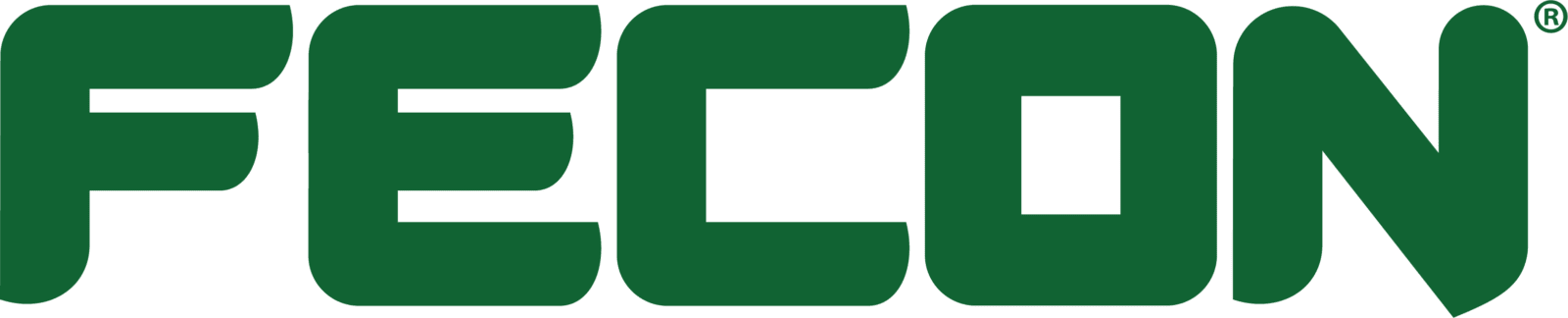
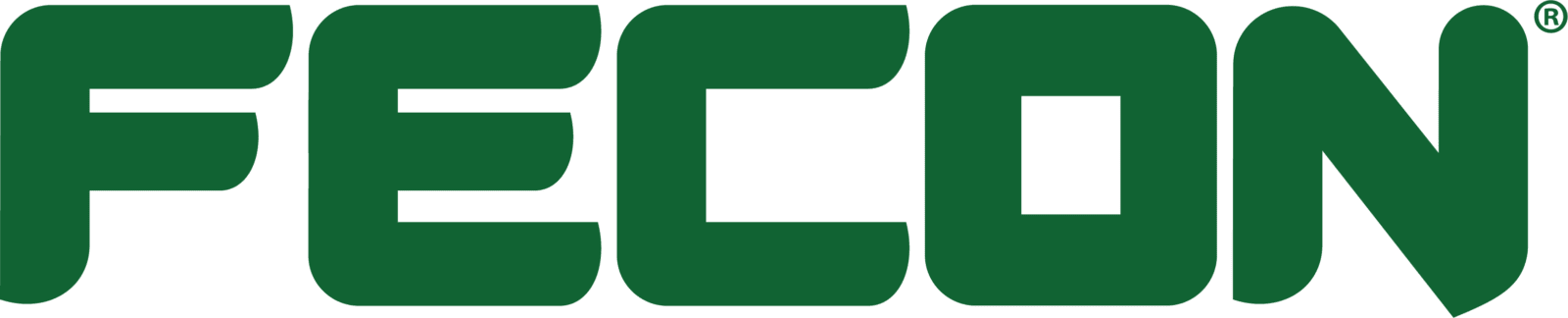
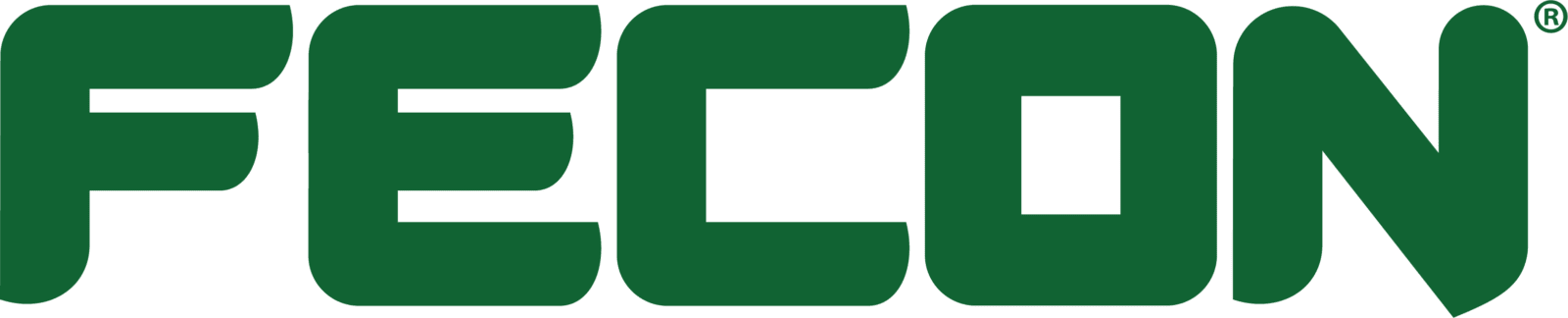
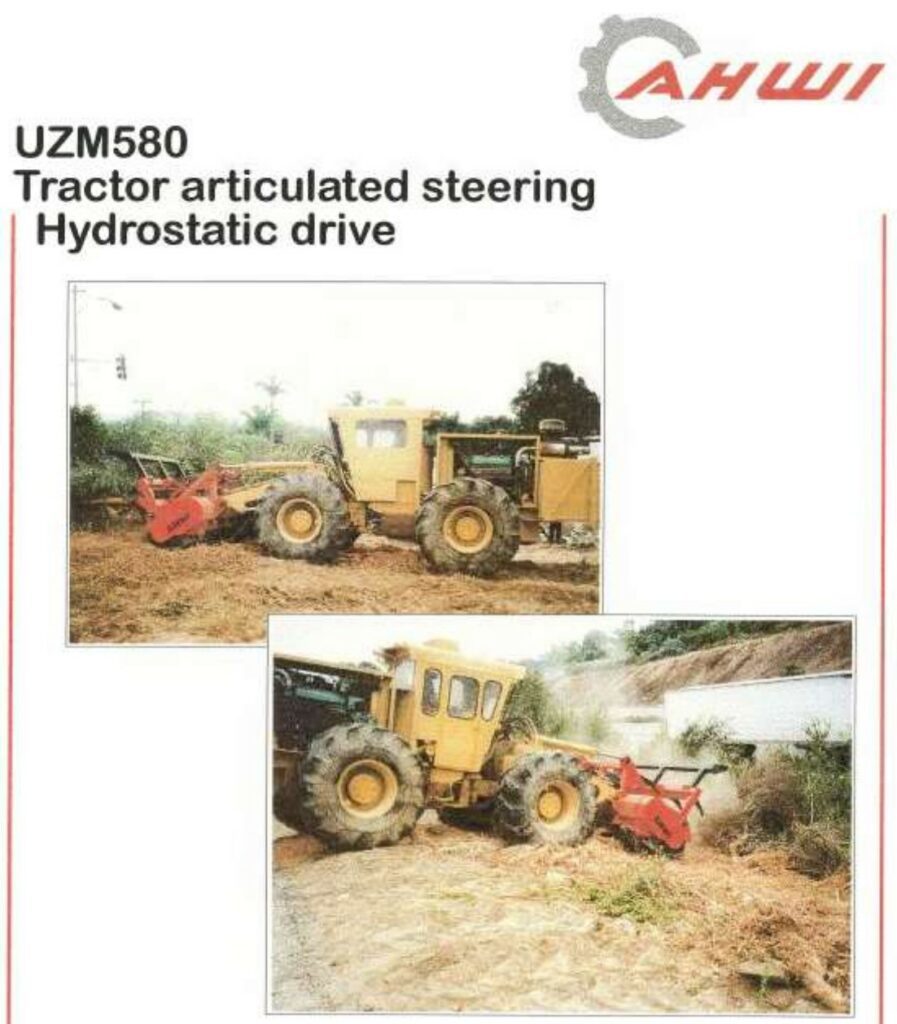
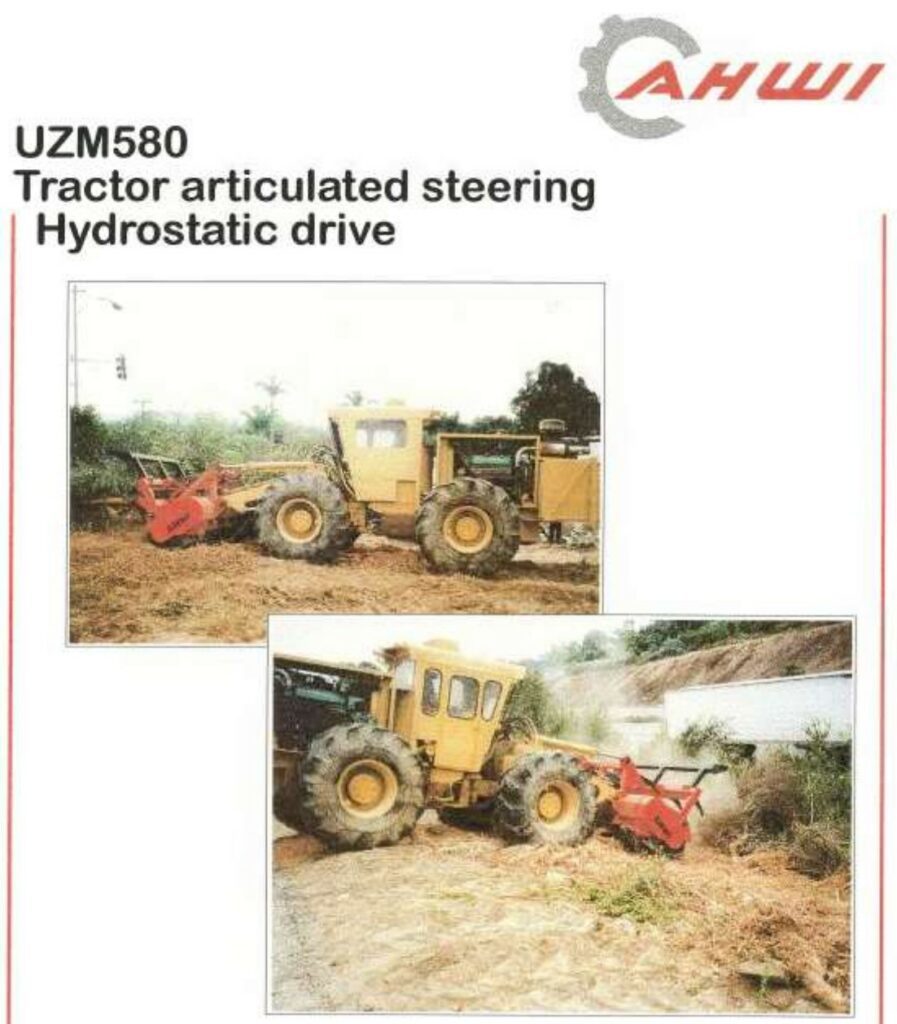



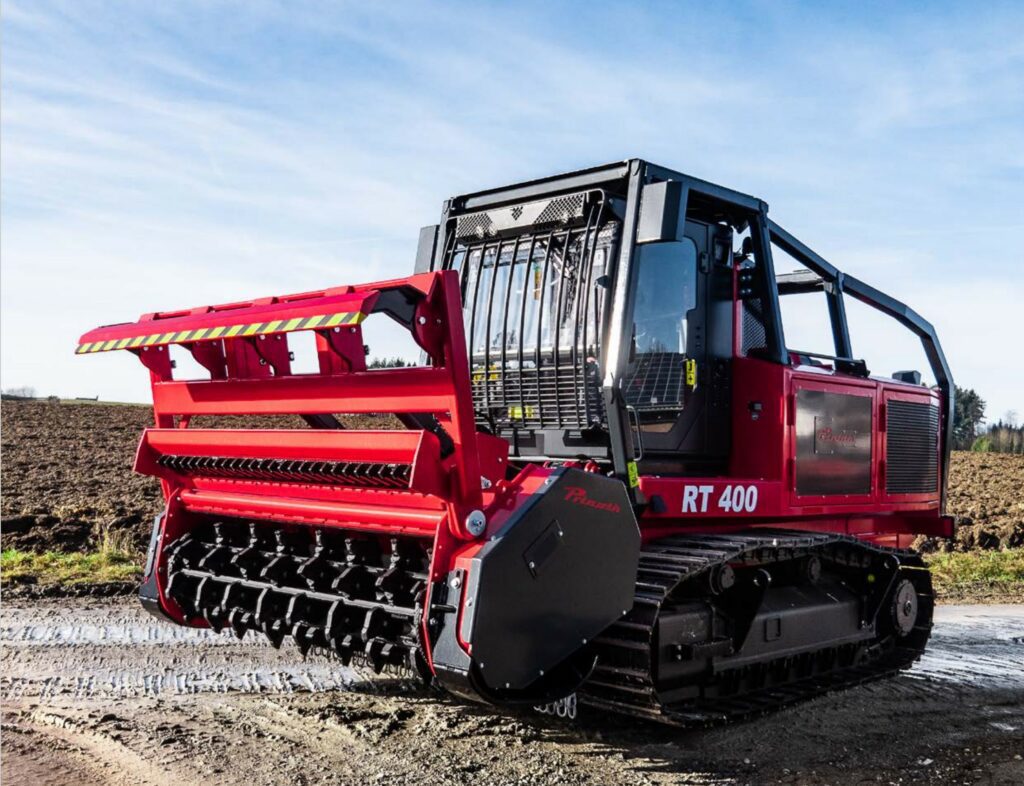
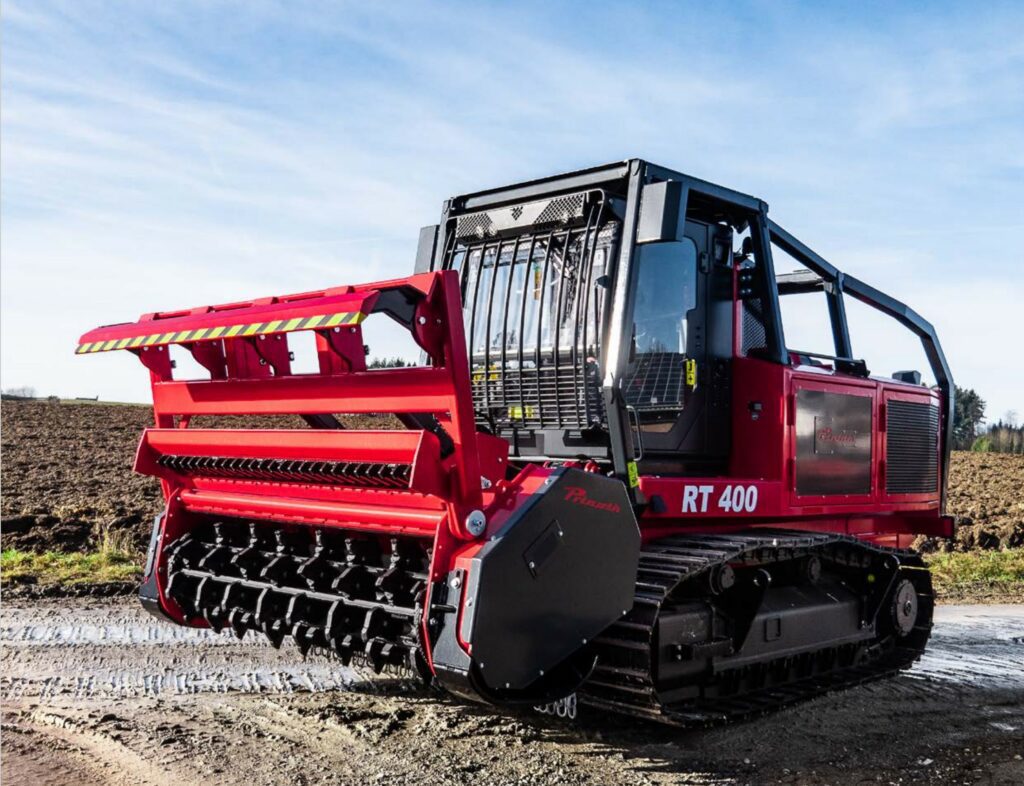
The basic rotor principle was used for many decades and rotor teeth had been updated and shaped which paved the way for forestry in many applications until today.
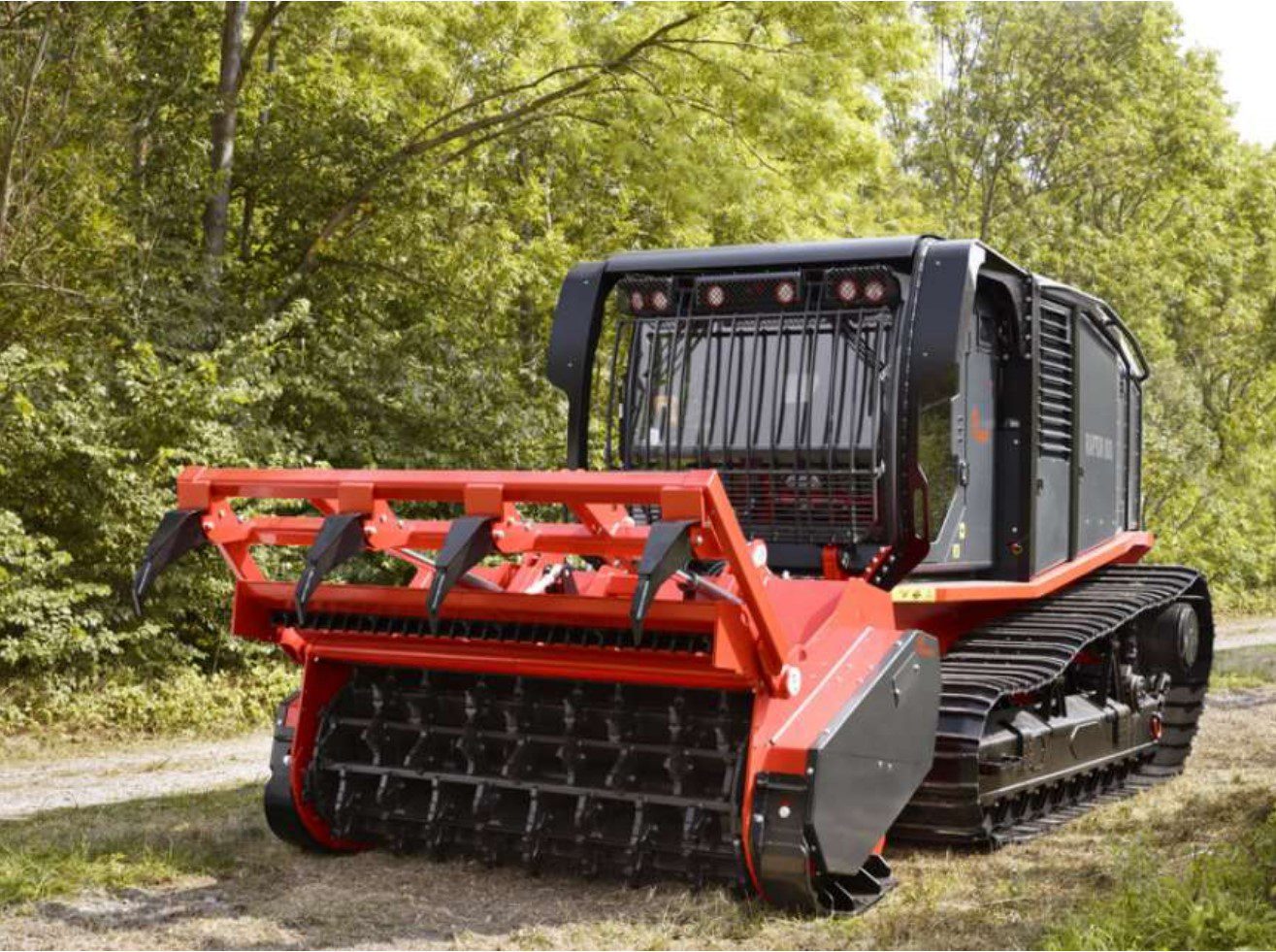
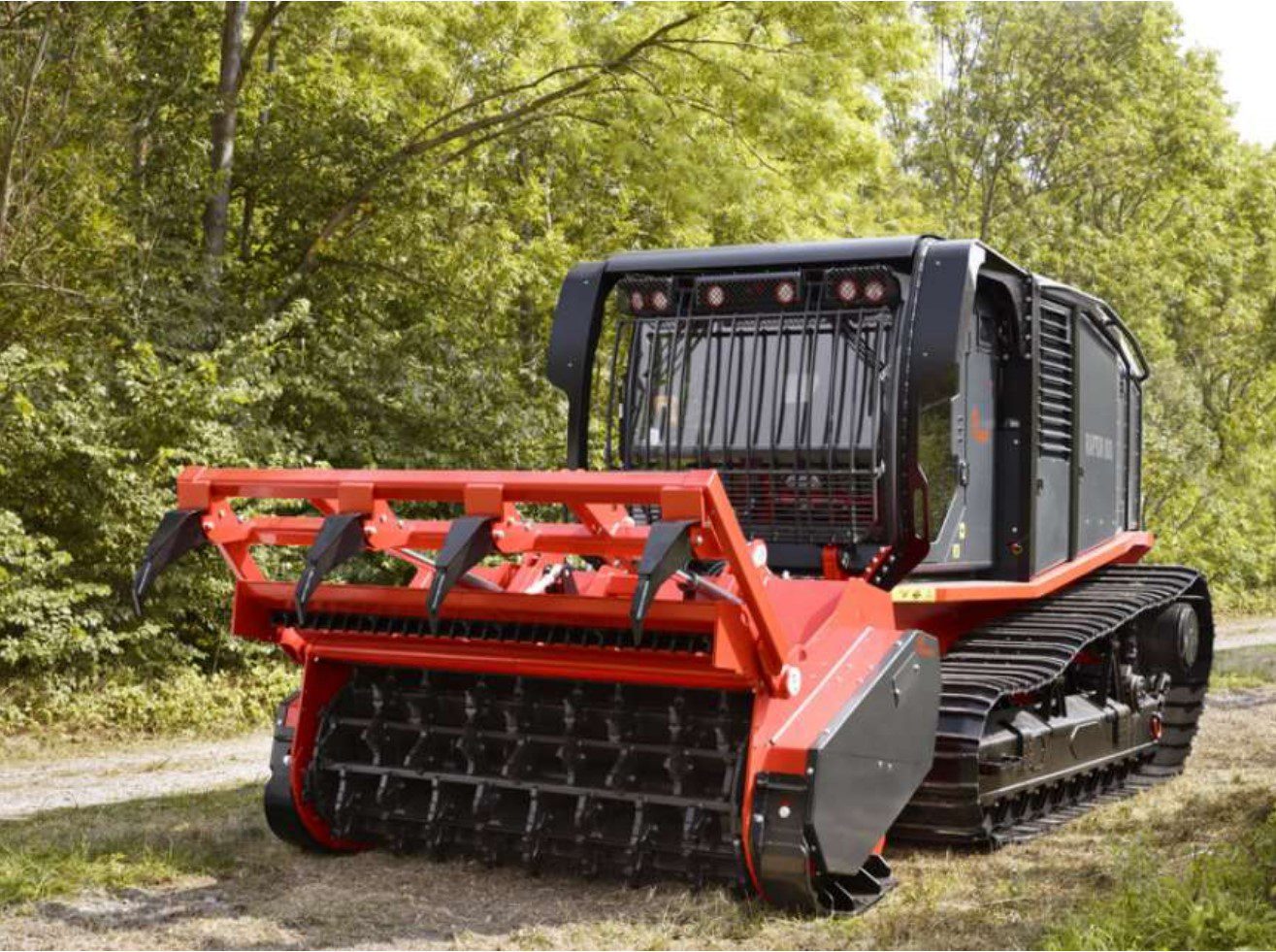
2004
Since 2004, many brands of vehicles dedicated to the use of mechanized brushcutting have appeared on the market. And as human nature wants, several companies have copied the concept of AHWI and FAE, and have arrived on the market of forestry mulching with carbide hammers and fixed hammers of various configurations.
Among these, the company Denis-Cimaf from Canada was acquired by Morbark in December 2018. Then, in 2019, in turn, Morbark was acquired by the Alamo Industrial Group.
AHWI was acquired by Prinoth in Austria and Fecon announced that Fecon was sold to to Windjammer Capital Investors in 2022.
MILITARY & NGO’s
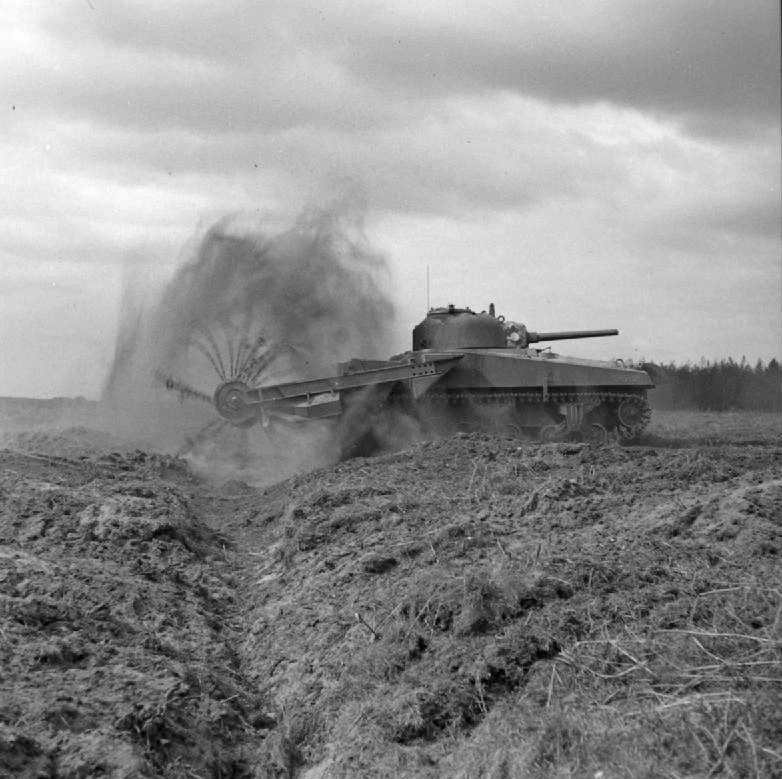
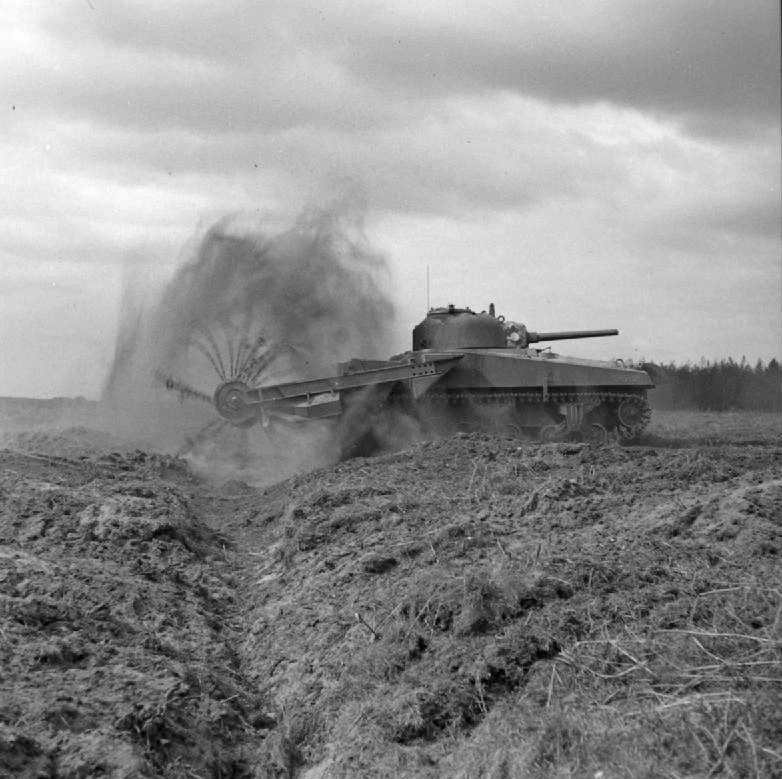
1940
the first tank was introduced with a flail system to destroy land mines
The M4 SHERMAN CRAB invented by British engineers
1997
The mine flail system was used in multiple applications since World WAR II, modern mechanical mine clearance started in the late 90’s with DOK-ING from Croatia, presenting their MV-1 mini flail system.
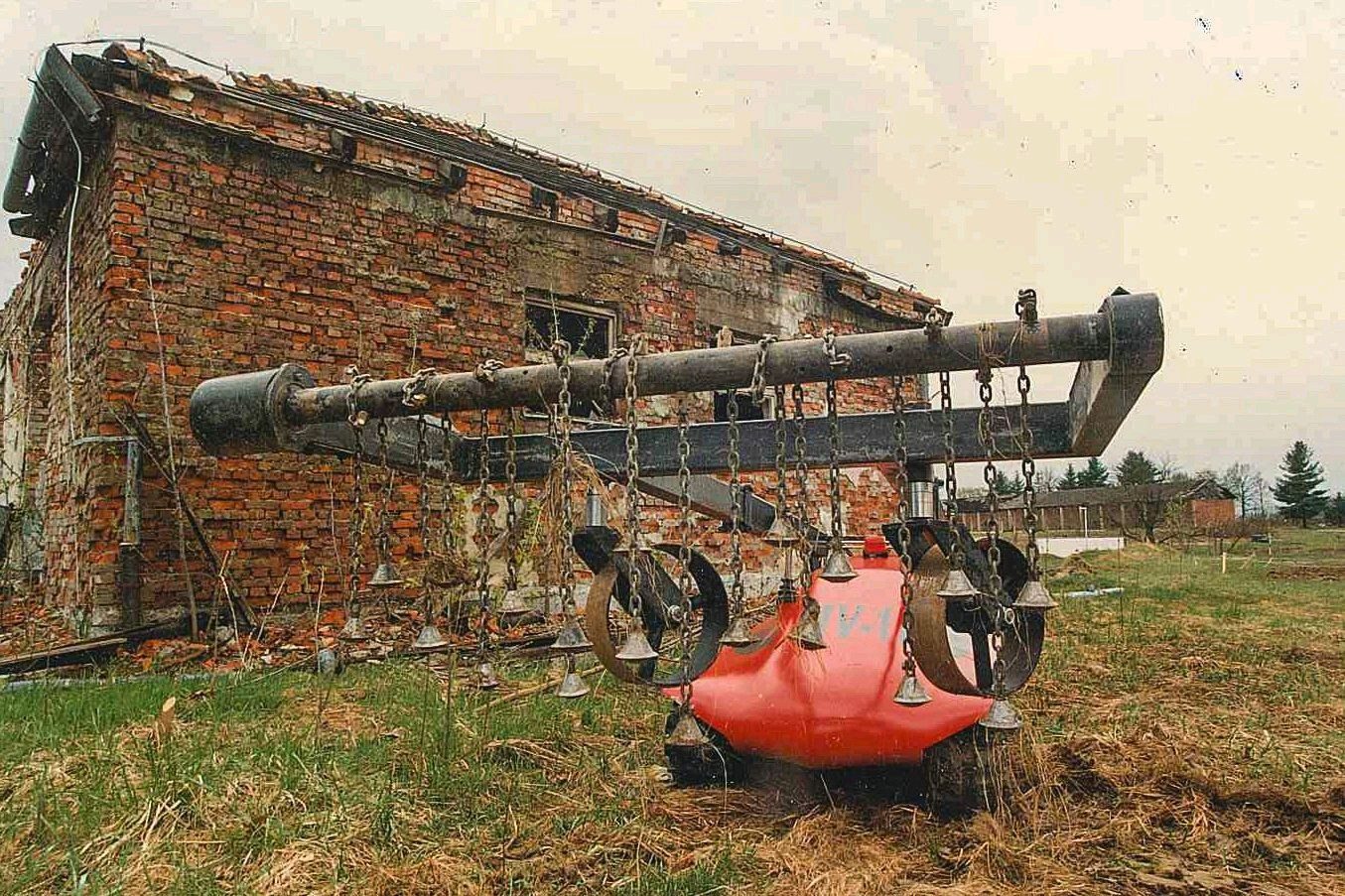
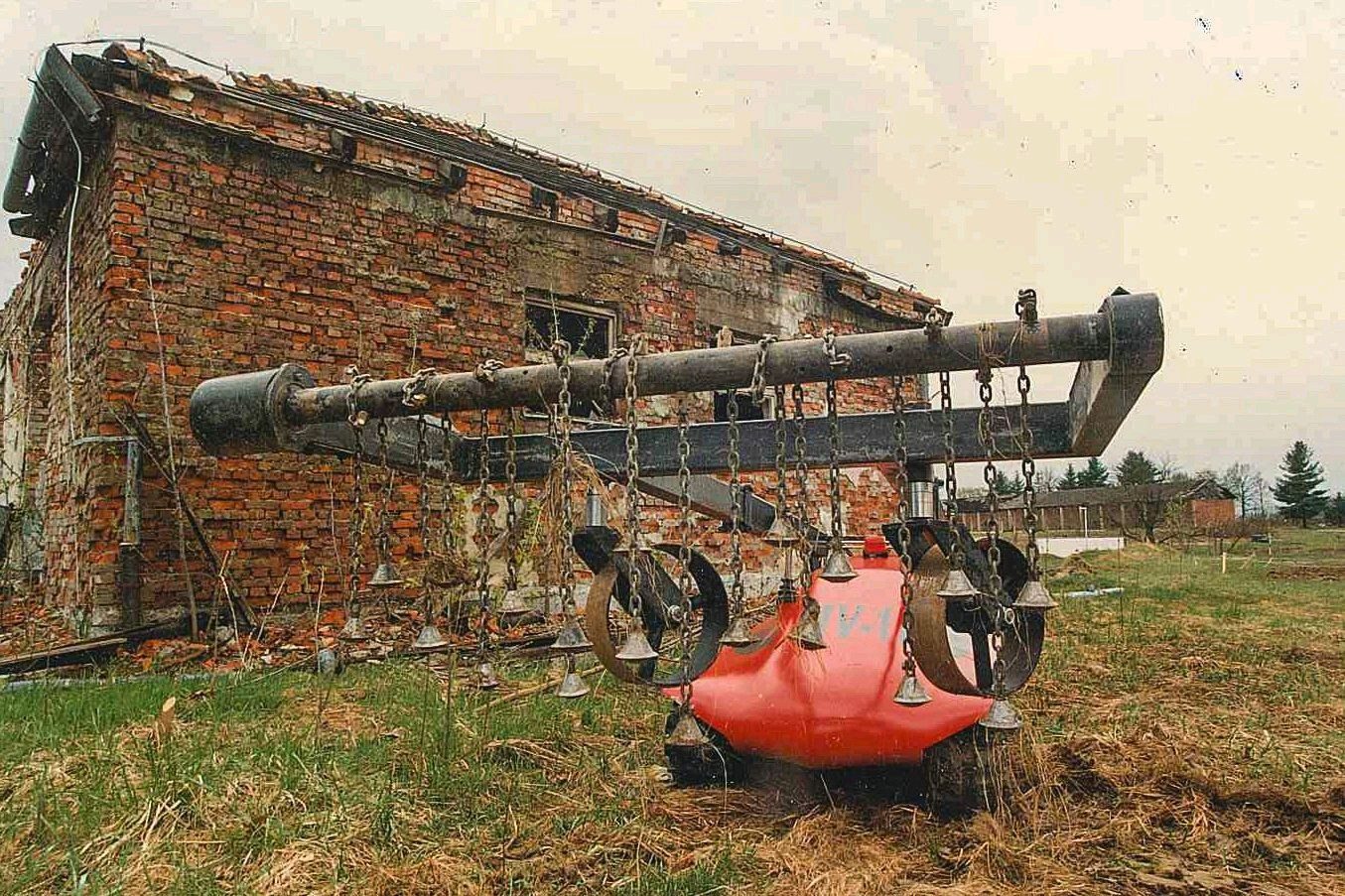
The U.S. Army used smaller, remote controlled units, such as the M160 or MV4.
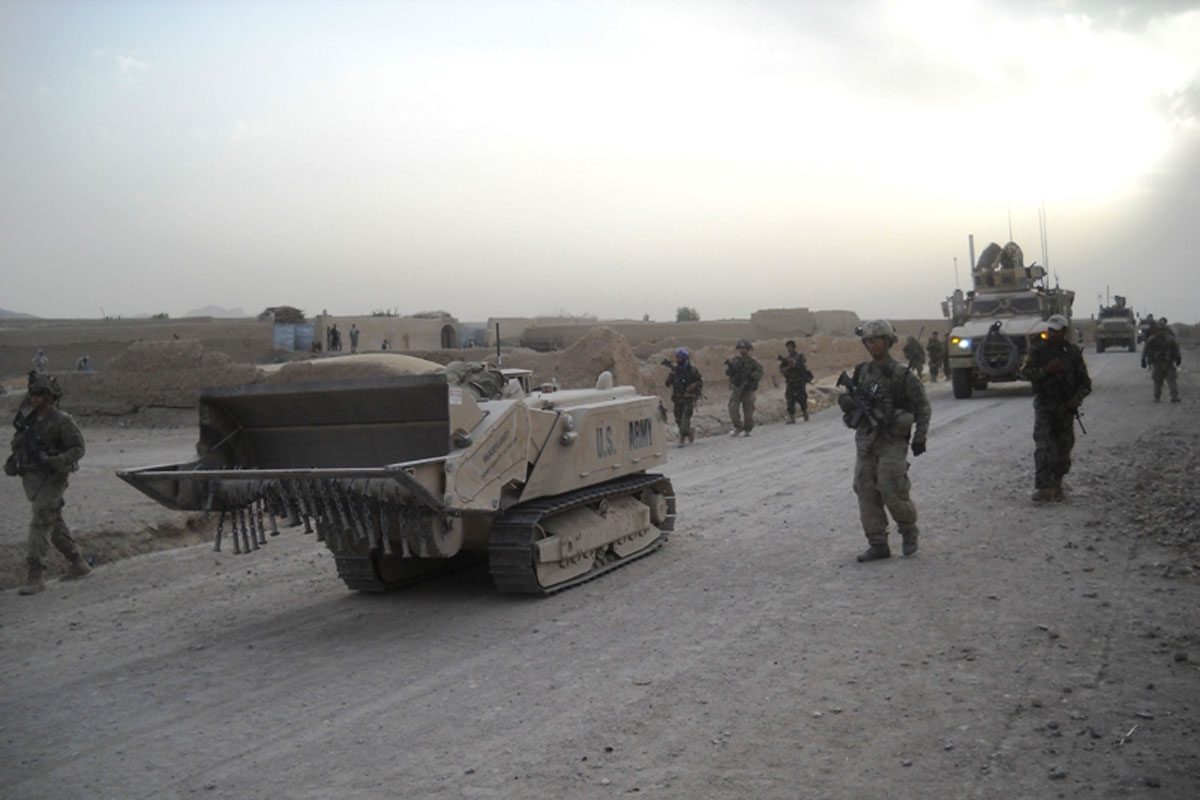
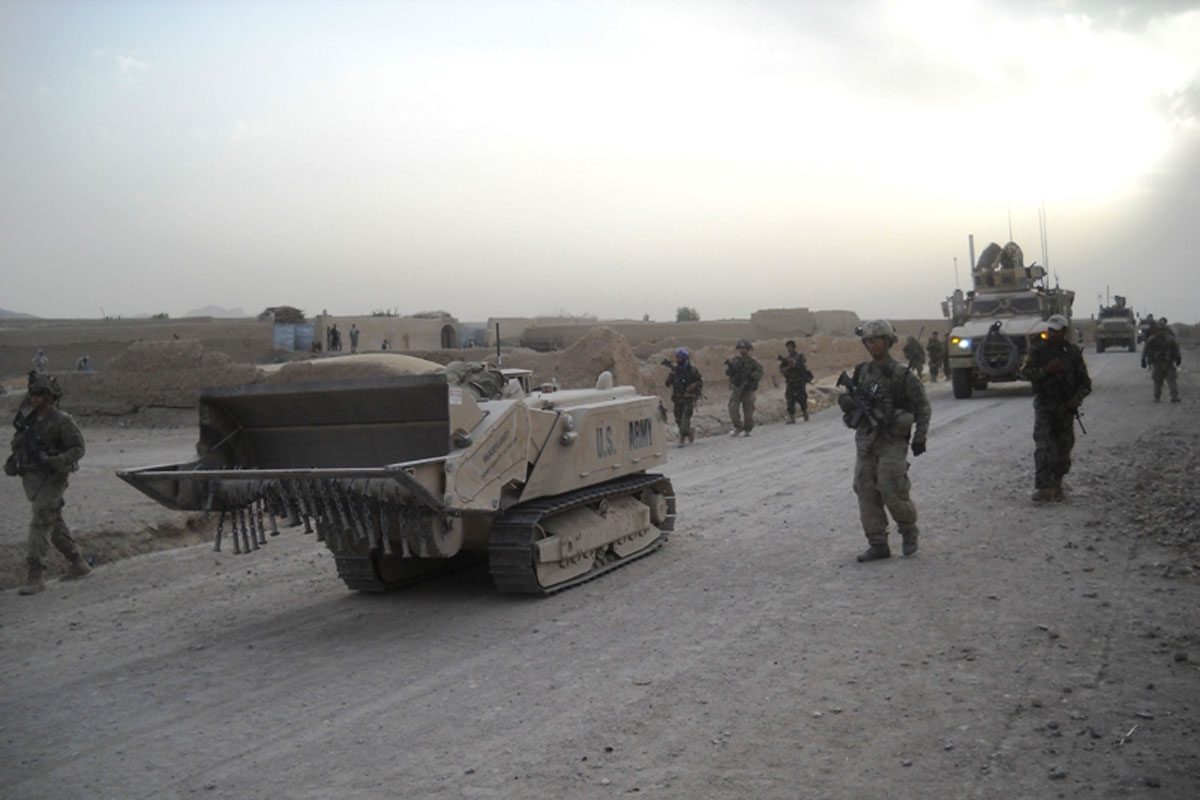
The US Army has been using the M160 remotely controlled flail robot built by the Croatian company DOK-ING in Afghanistan for route clearance missions.
1998
Inspired by the new rotor system of AHWI (see forestry), the first design steps for the MineWolf mine clearance machine were made in 1998 based on a concept by Heinz Rath


of integrating a commercial platform with a tiller (fixed rotor design). But before the new rotor took over, all machines had been build with the mine flail tool.
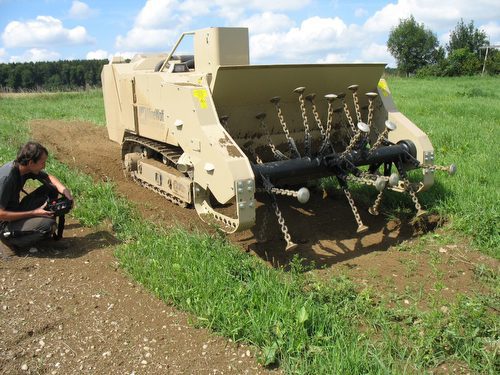
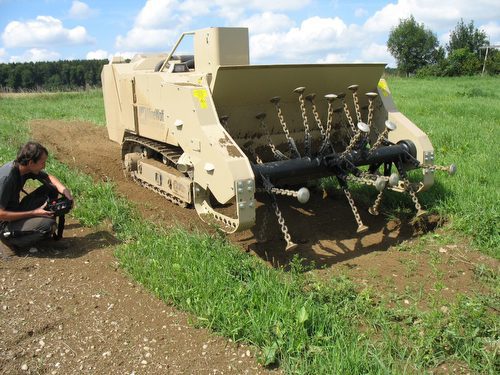
MW240
With FL194 Mine Flail
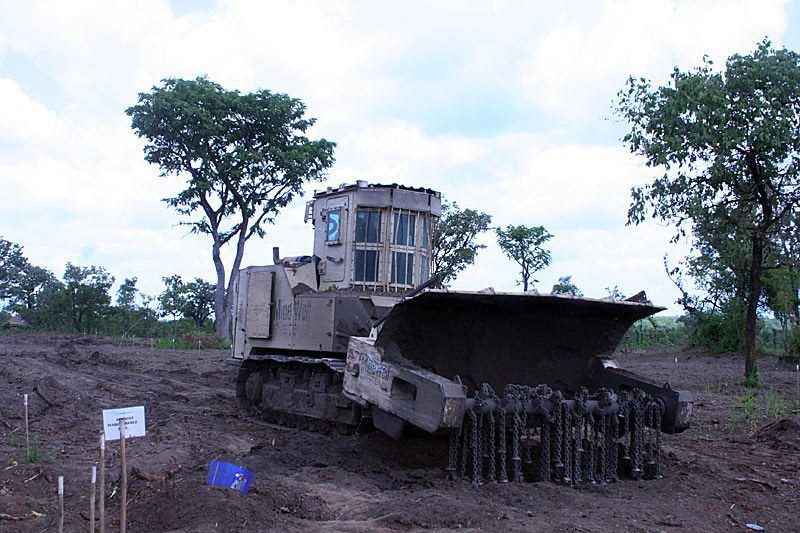
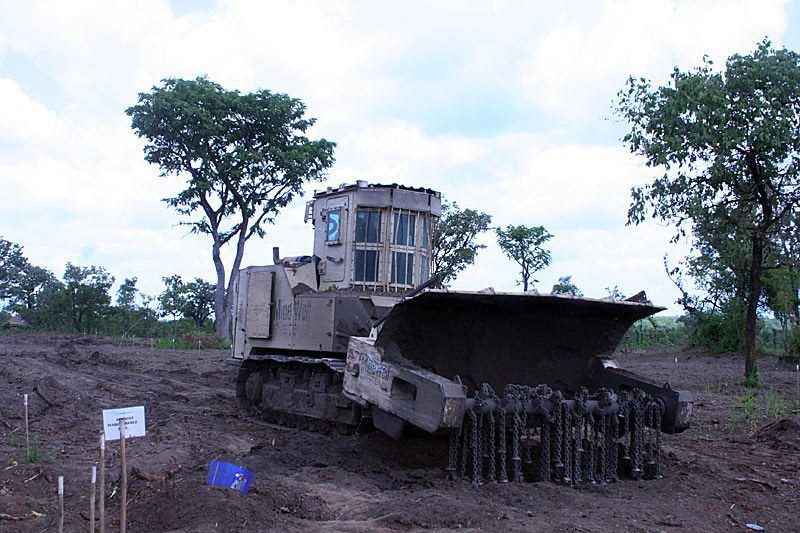
MW370
With FL280 Mine Flail
The first prototype was constructed by consortium under the leadership of RUAG in the production facilities of AHWI.
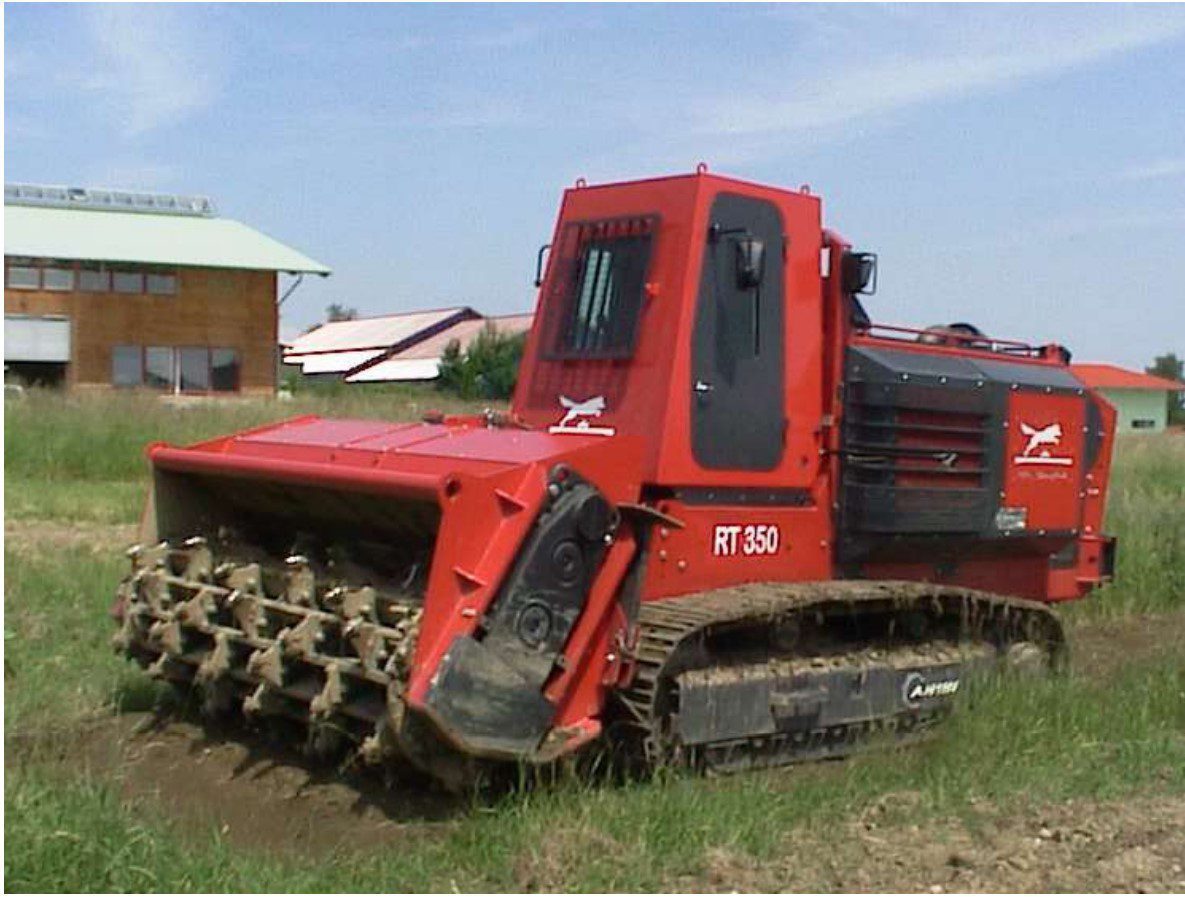
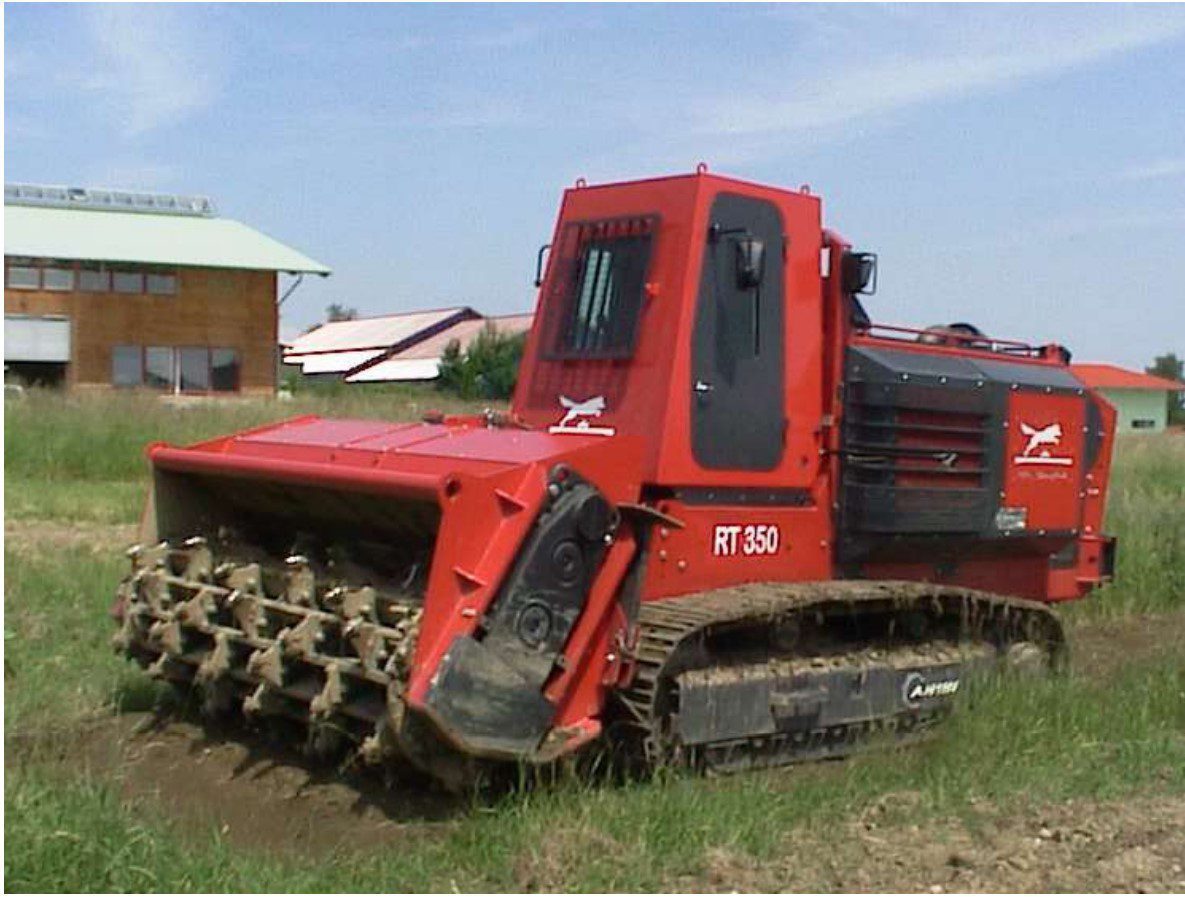
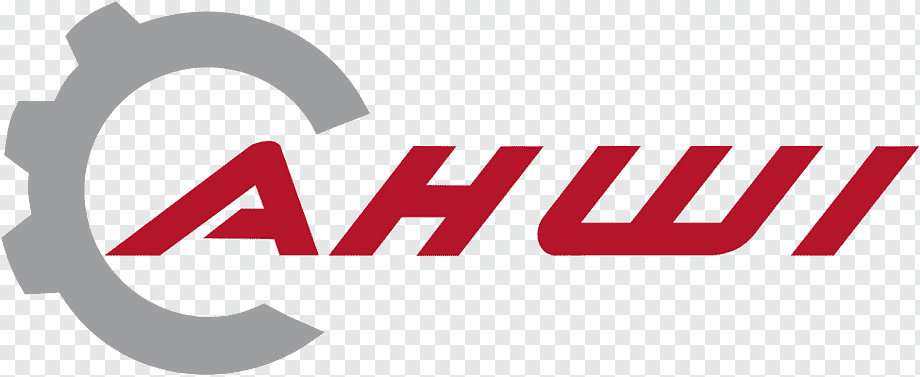
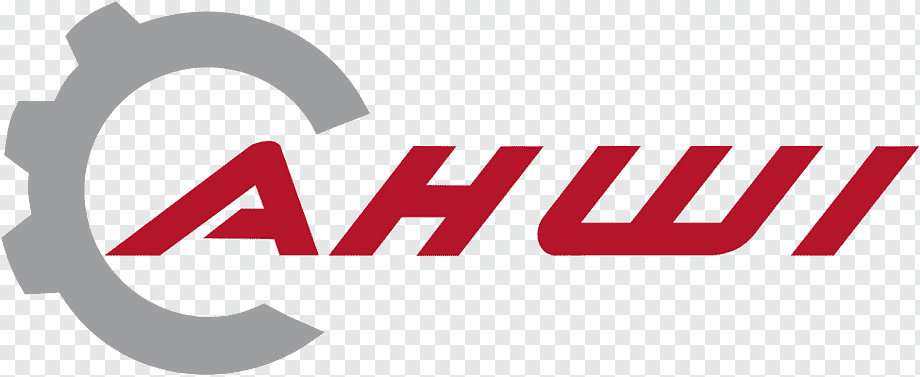
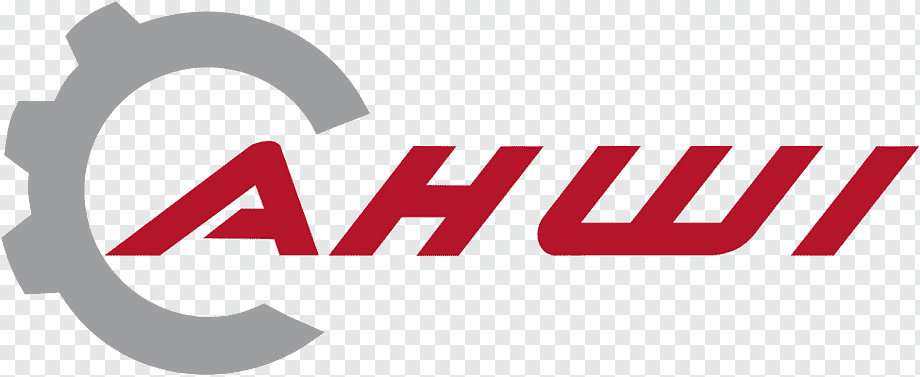
2001
In 2001 the first platform was developed and tested and the final MineWolf prototype was built.
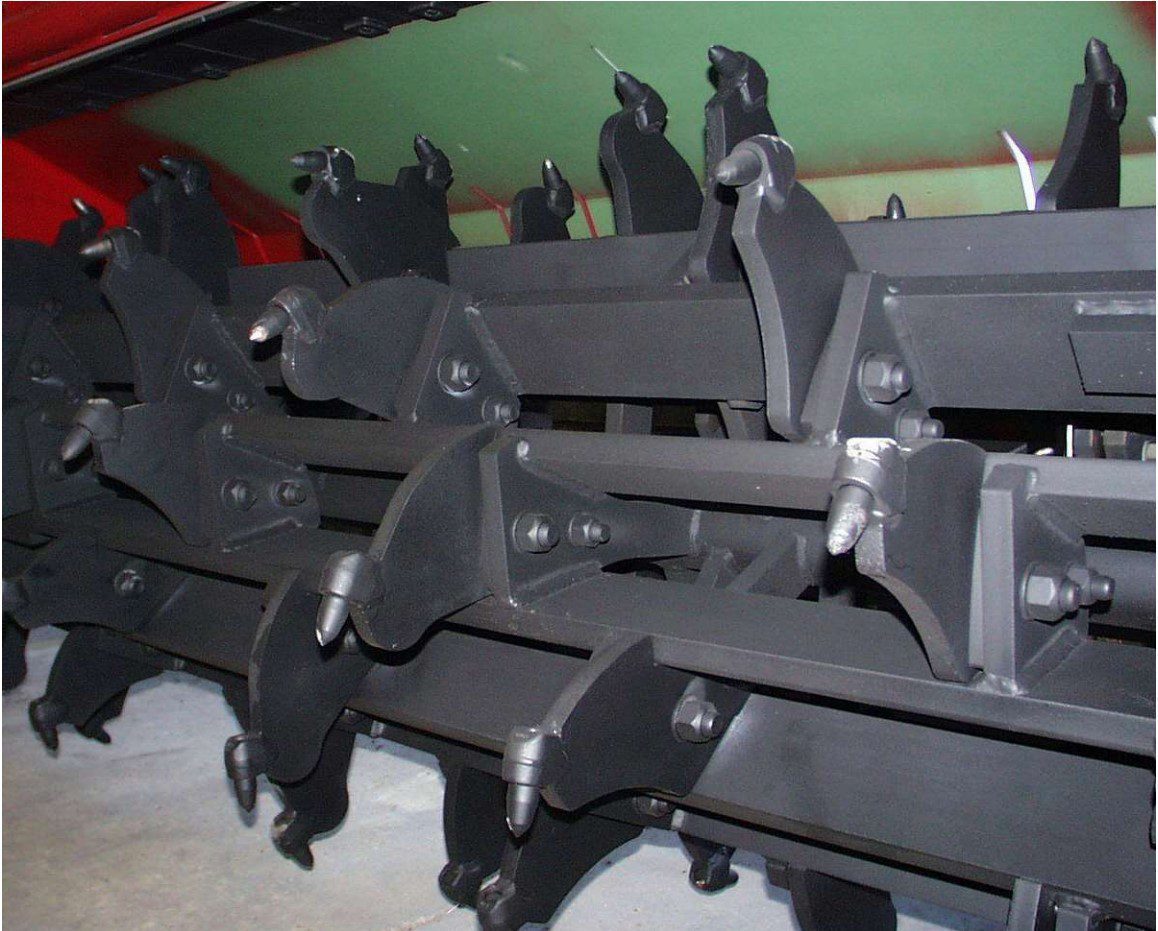
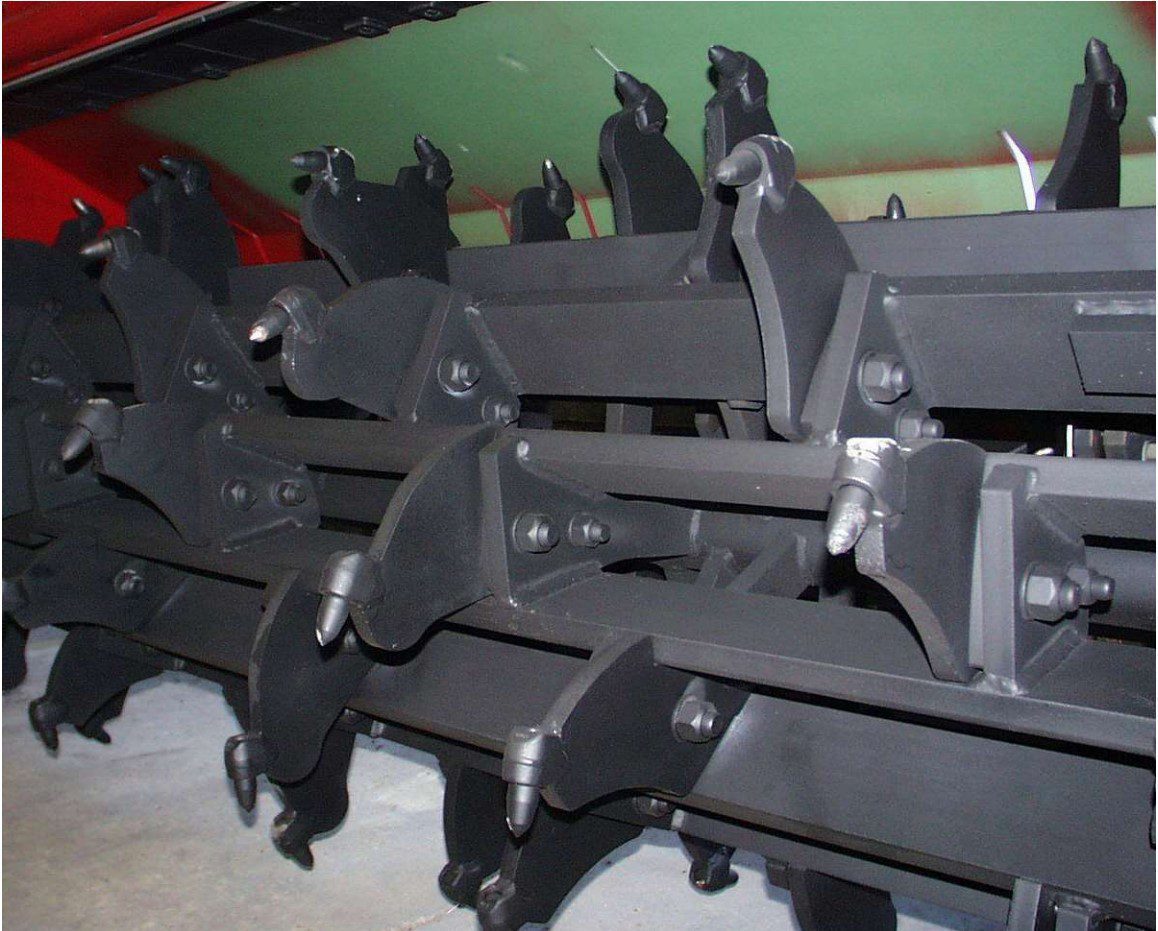
The core rotor principle was the same as applied with subsoilers (see FARMING section) but with an open rotor design to make sure the blast of mine detionations could escape without resistance or major damage to the rotor (Video). It was successfully deployed for anit-personnel and anti-tank mines.
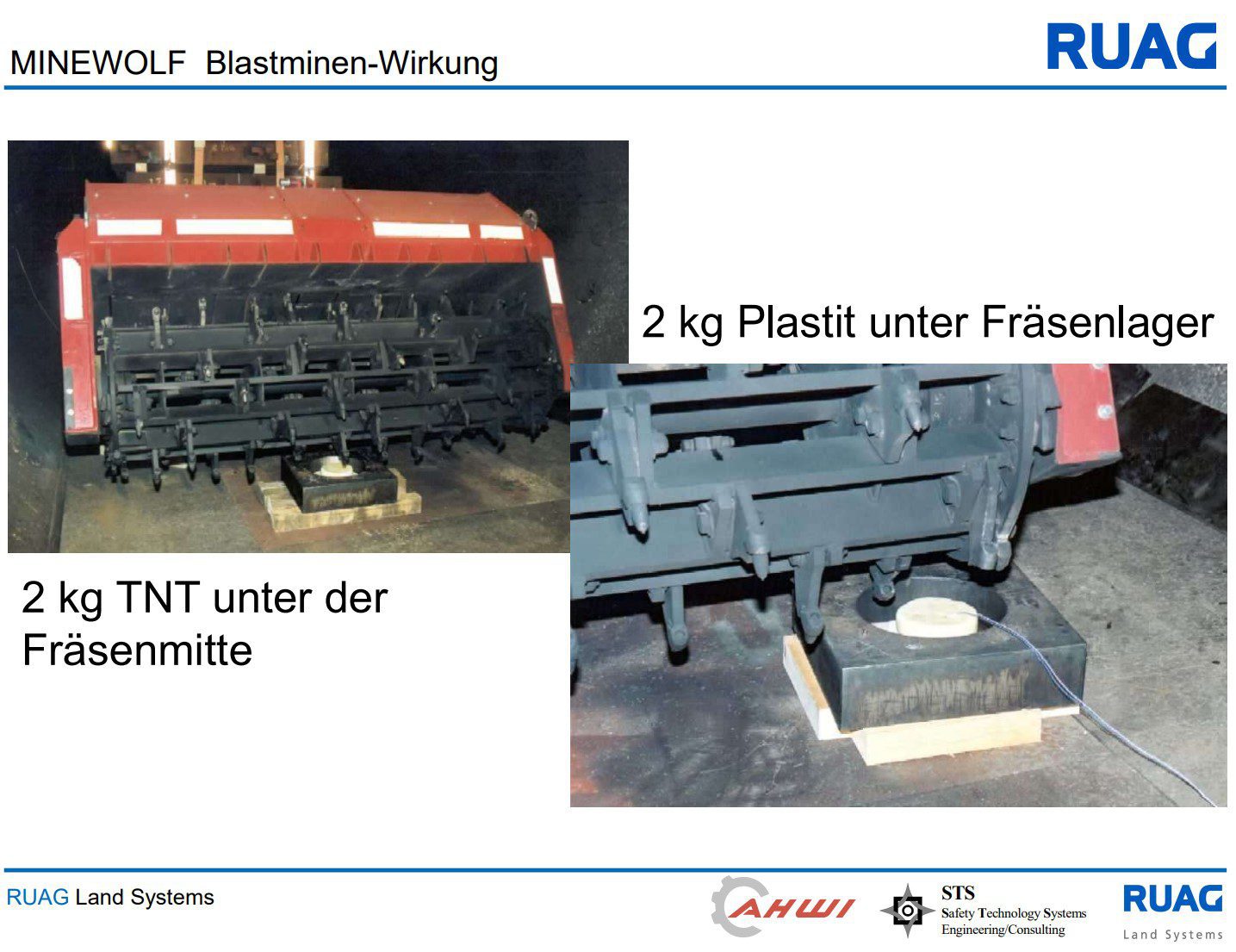
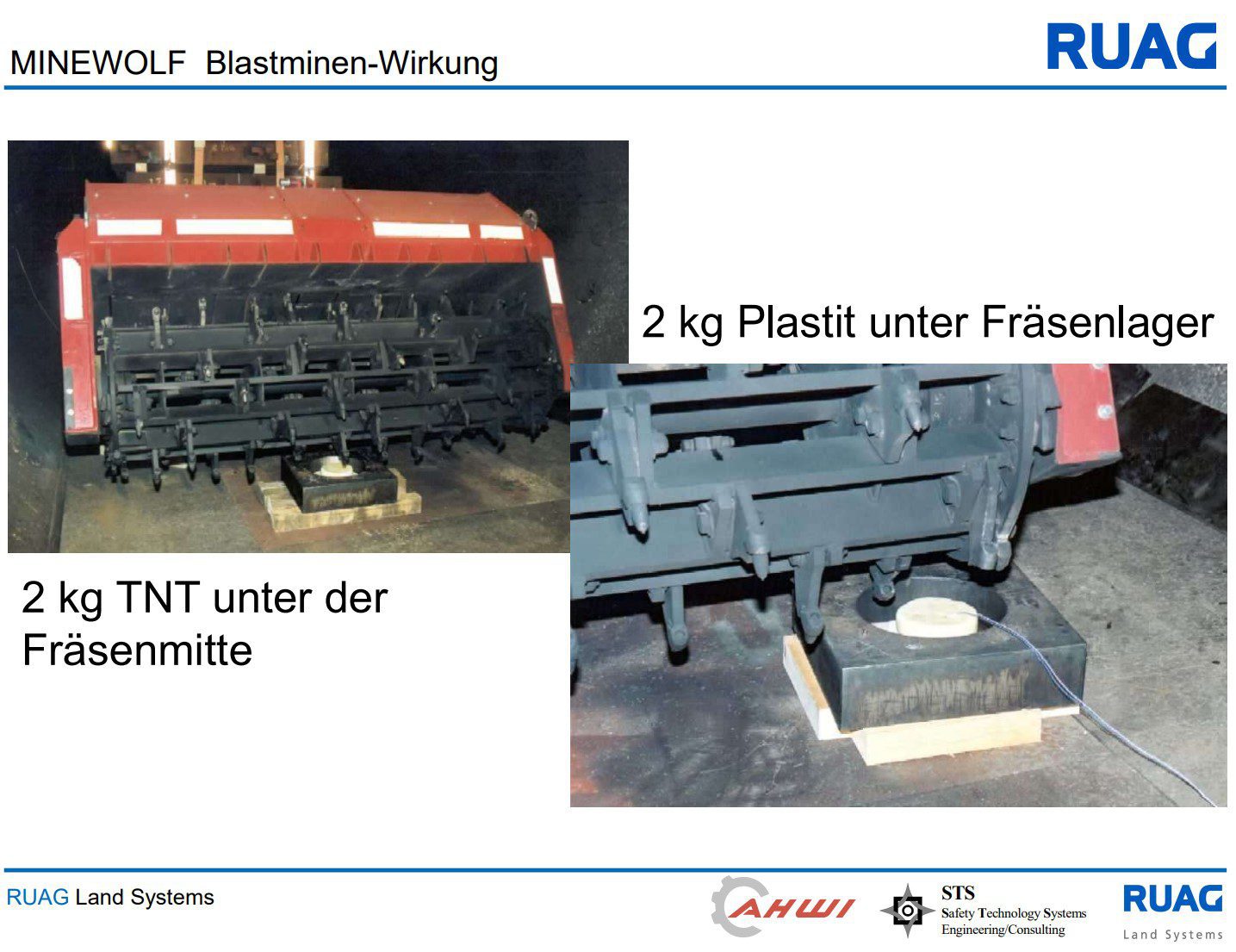
It was accredited by the German Army in 2004.
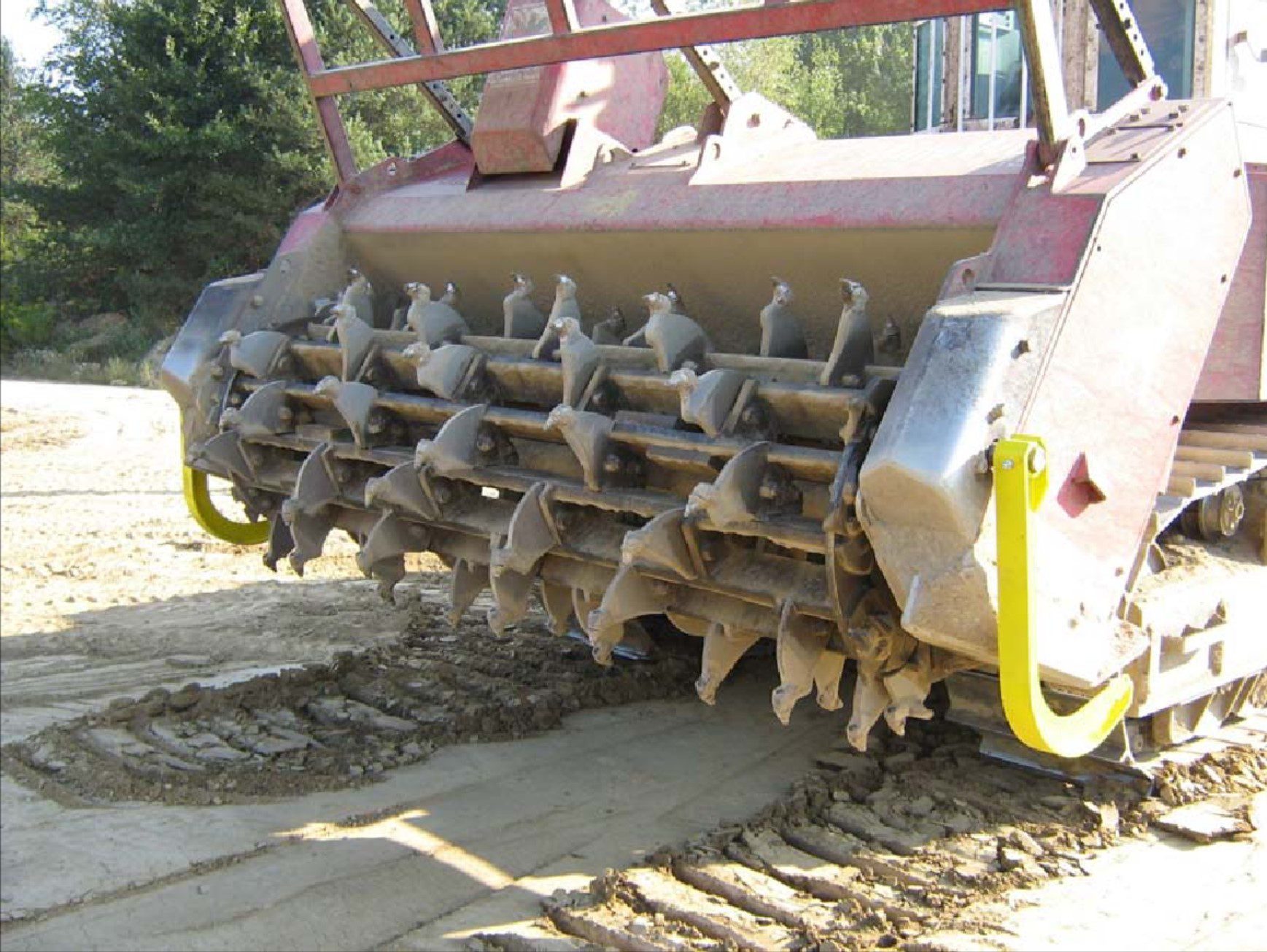
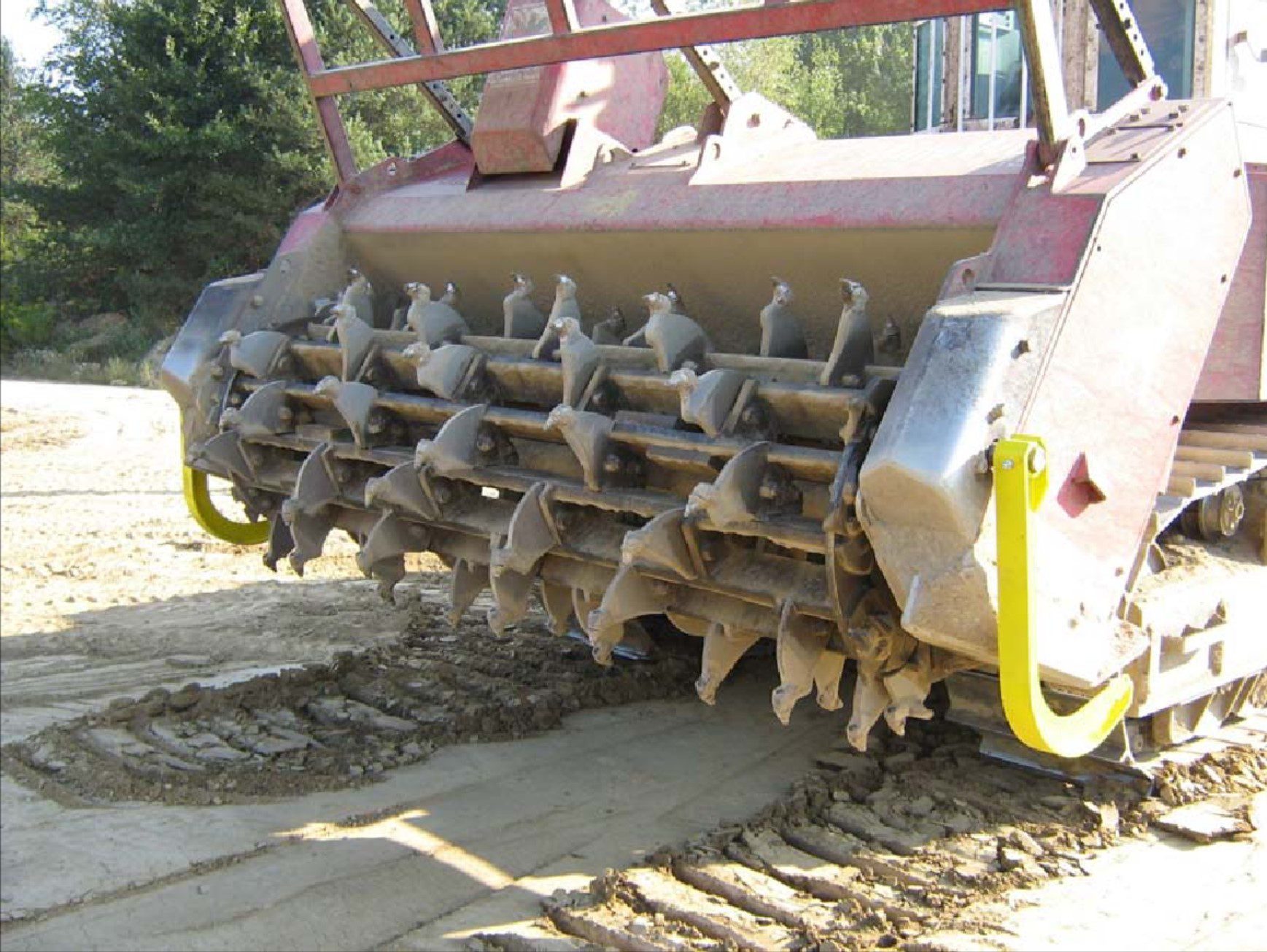
The same year that MineWolf Systems GmbH was founded.
2004
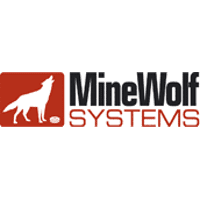
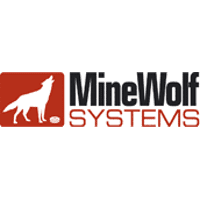
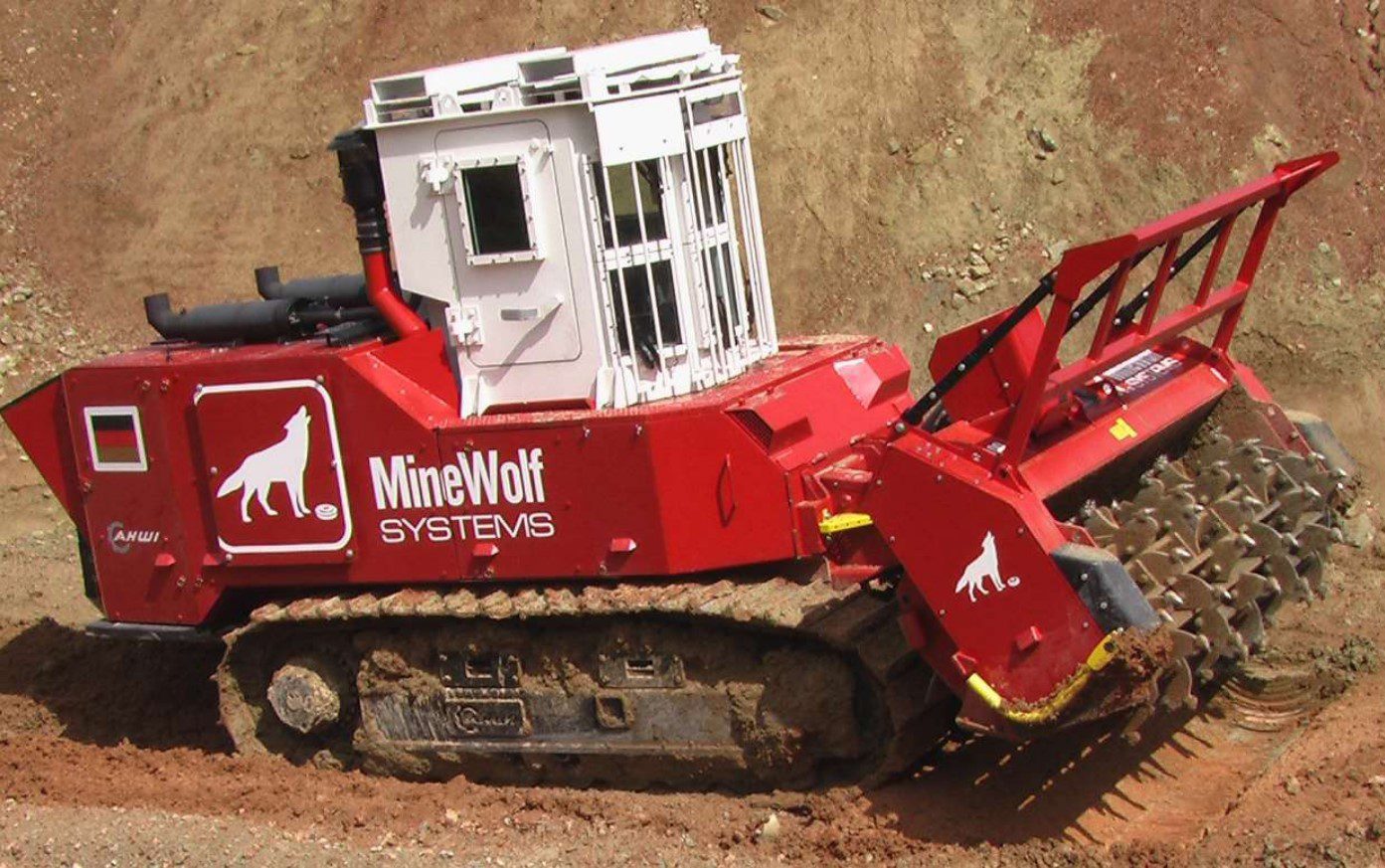
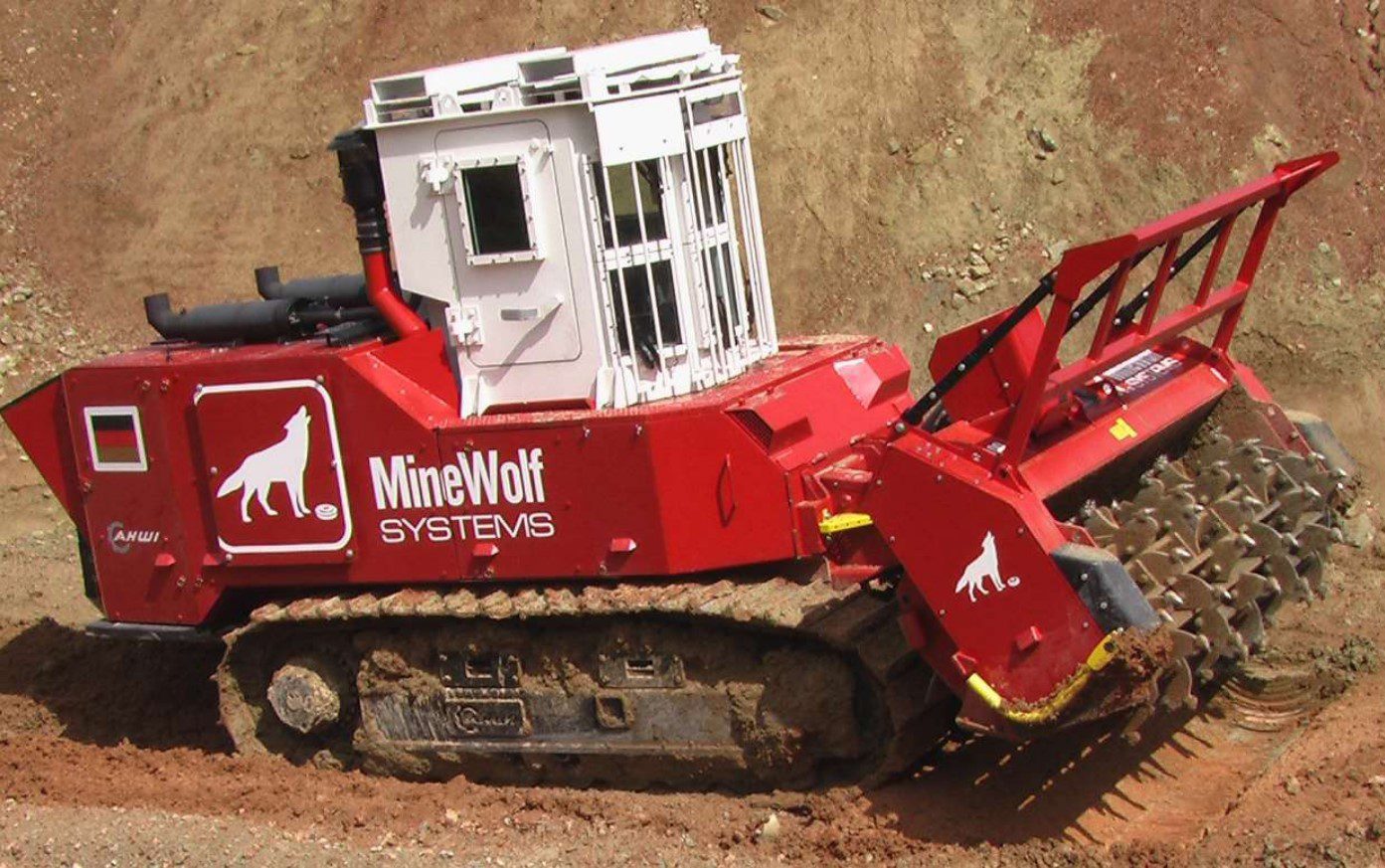
2005
The new rotor design was a huge success which paved the way for military and NGO applications to use the new rotor with fixed tools and carbide tips for mechanical mine clearance applications. The platforms are used by humanitarian and commercial mine clearance agencies and governments.
They are used by the British Army and the German Bundeswehr for route clearance, i.e. clearing IEDs and mines from routes in Afghanistan and by the United Nations Mine Action Service and MINUSMA peacekeepers for IED clearance